---skyscraper.jpg?sfvrsn=2)
- Training details
Card payment issues
While we resolve some issues with card payments via our website, please follow one of these options if wish to book training using a credit card:
1. Follow the checkout process and click "Pay later" OR 2. Contact us at [email protected].
We’ll then get in touch as soon as possible to process your payment.

8D Problem Solving
Learn to identify, correct and eliminate recurring problems.
Next available: London, 07 Nov 2024
Members: £ 550 + VAT Non-members: £ 650 + VAT
8D is a team-based problem-solving methodology that was originally used in the automotive industry but is now used in a wide range of industry applications. It is designed to put a short-term fix in place, find the real root cause of a problem and implement a permanent long-term solution.
This highly practical and interactive course focuses on ensuring you can implement the 8D methodology and problem-solving tools immediately and apply it in a variety of scenarios, from shop floor staff needing to use the tools as part of problem-solving teams; to managers looking to drive improvements.
Who should attend?
How will i benefit.
- Have greater knowledge of the principles of problem solving
- Understand the nine steps of 8D and the importance of working as a team
- Understand the importance of using data to support 8D problem solving
- Be able to implement the 8D approach to problem solving to support your work activity
- The importance of a structured problem-solving approach
- Overview of 8D and its aims and objectives
- A detailed view of each level of the 8D methodology
- Common aspects of problem solving that link to 8D
- Considerations for roll out of the 8D approach in your organisation
Mapped against UK- SPEC competencies: B and E
- Design and development of processes, systems, services and products - For Chartered Engineers: ‘Apply appropriate theoretical and practical methods to the analysis and solution of mechanical engineering problems’ For Incorporated Engineers ‘Apply appropriate theoretical and practical methods to design, develop, manufacture, construct commission, operate, maintain, decommission and re-cycle mechanical engineering processes, systems, services and products’
- Professional commitment - For Incorporated and Chartered Engineers: ‘Demonstrate a personal commitment to professional standards, recognising obligations to society, the profession and the environment’
Meet our trainers
These trainers regularly teach 8D Problem Solving.
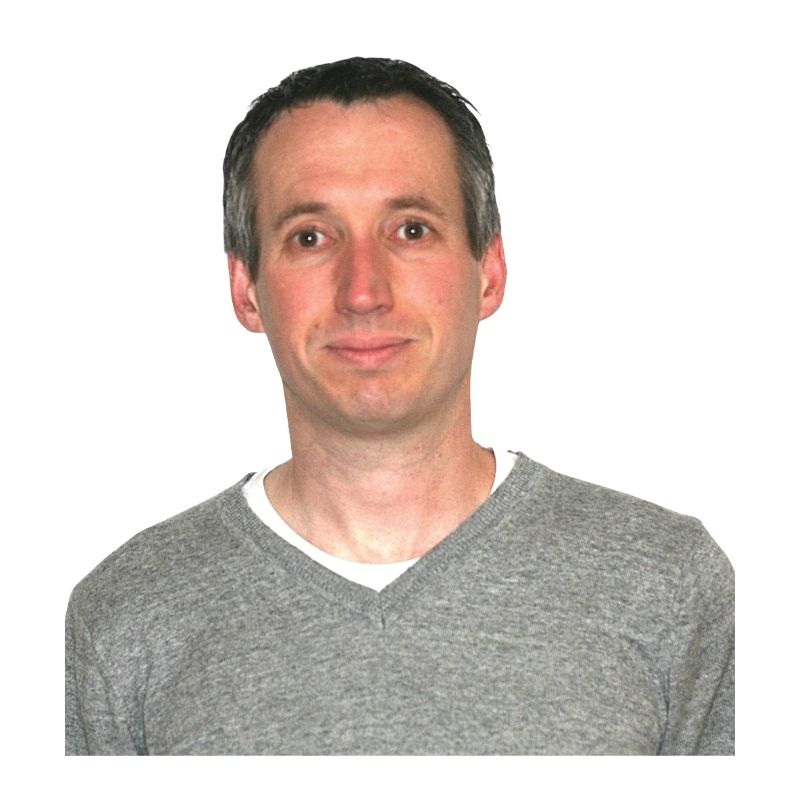
Mike O'Connell
In-house and bespoke training.
Tell us your team's CPD needs and we'll come to you with a specialised training programme, customised for your engineering sector. Contact our advisors if you need help finding the most appropriate training for your team.
- [email protected]
- + 44 (0)20 7304 6907
- Enquire Now
At a glance
- Duration: 1 day
- Location: London
- CPD Hours: 7
- UK-Spec: B, E
Need some help?
Contact us if you have any questions about our training courses.
- +44 (0)20 7304 6907
Terms & conditions of booking IMechE training
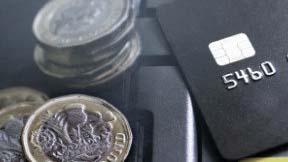
Offers and bundles
A range of options to help you maximise your training budget.
Available dates for 8D Problem Solving
1 day course
Require a different date or location? Or want to train a group in house?
We can customise any of our courses and deliver them in-house, for your entire team. It could also save you money, especially as you would save travel time.
More about In-house and bespoke training
Register your interest
Members: £ 550 + VAT
Non-members: £ 650 +VAT
Enquire now
Train a group in-house and save
Train your team
Tell us your team’s development needs and we’ll come to you with a specialised training programme, customised for your organisation.
What options are available?
- Off the shelf – we can deliver any of our training courses at your chosen location, providing you with a cost-effective and efficient solution
- Tailored courses – our personalised programmes can help you work through issues specific to your team or sector and equip you with the practical tools you need to move forward
- Blended programmes – we use a range of delivery methods, development subjects and performance resources to ensure your team have the knowledge and skills they need to help your business thrive
More about in-house and tailored training .
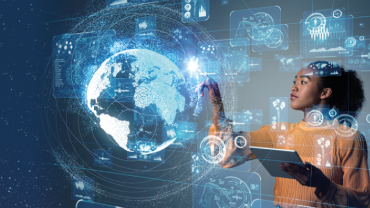
Request a Training catalogue
Discover the most extensive series of professional development courses for engineers who are committed to shaping the future of our sector.
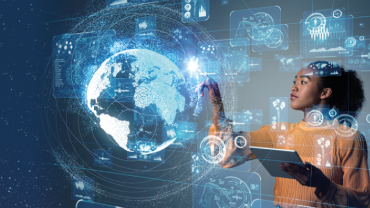
Some of the companies we've worked with
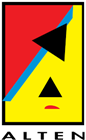
Our training acumen
- Over 30 years of experience delivering training
- More than 200 courses designed for engineers
- Over 10,000 engineers trained each year
- Trusted by over 800 companies
- Business solutions delivered in 48 countries
Average customer rating: 4.75 out of 5
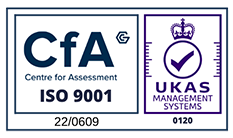
Get in touch
Get in touch if you need help finding the right course, or qualification, for you or your team.
- Request a brochure
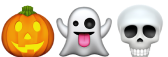
- Onsite training
3,000,000+ delegates
15,000+ clients
1,000+ locations
- KnowledgePass
- Log a ticket
01344203999 Available 24/7
8D Problem Solving Training Course - United Kingdom
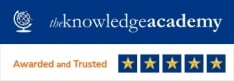
- Gain in-depth knowledge of the principles and framework of 8D Problem-Solving.
- Acquire the necessary skills for implementing the techniques of root cause analysis.
- Understand how to develop and evaluate effective corrective actions.
8D Problem Solving Training Course Overview
- Course syllabus
- Who it’s for
- What’s included
- Why choose this course
8D Problem Solving Training Course Outline
Module 1: Introduction to 8D Problem Solving
- Overview of the 8D Methodology
- Benefits and Importance of 8D Problem Solving
- Key Terminology in 8D Problem Solving
Module 2: Define the Problem (D1 and D2)
- Defining the Problem Statement
- Gathering Information and Data Collection
- Identifying the Scope of the Problem
- Setting Clear Objectives and Goals
Module 3: Establishing the Team (D3 and D4)
- Forming the Problem-Solving Team
- Roles and Responsibilities of Team Members
- Effective Communication within the Team
- Team Dynamics and Collaboration
Module 4: Root Cause Analysis (D5 and D6)
- Introduction to Root Cause Analysis
- Tools and Techniques for Identifying Root Causes
- Five Whys Analysis
- Cause and Effect Diagrams
Module 5: Implement Corrective Actions (D7)
- Developing and Evaluating Possible Solutions
- Selecting the Most Feasible Corrective Actions
- Planning and Implementing the Corrective Actions
- Monitoring and Measuring
Module 6: Prevent Recurrence (D8)
- Importance of Preventive Measures
- Designing and Implementing Preventive Actions
- Verification and Validation of Preventive Actions
- Continuous Improvement and Lessons Learned
Module 7: Documentation and Reporting
- Importance of Documentation in 8D Problem Solving
- Effective Reporting Formats and Templates
- Documenting the Problem-Solving Process
- Presenting Findings and Recommendations
Who should attend this 8D Problem Solving Training Course?
The 8d problem solving training course is designed for individuals across various roles who want to learn the structured approach of the 8d (eight disciplines) problem-solving methodology. this course is beneficial for various professionals including:.
- Quality Control Professionals
- Process Improvement Specialists
- Operations Managers
- Manufacturing Professionals
- Quality Assurance Engineers
- Six Sigma Practitioners
- Risk Management Specialists
Root Cause Analysts
Prerequisites for the 8d problem solving training course.
There are no formal prerequisites for attending this 8D Problem-Solving Training Course.
8D Problem Solving is a systematic and structured approach used to identify, analyse, and resolve complex problems within an organisation. 8D Problem-Solving methodology is crucial for organisations as it enables them to proactively address challenges, improve processes, and enhance overall performance. 8D Problem-Solving Training Course is beneficial for an organisation as it enhances problem-solving capabilities, promotes cross-functional collaboration, and empowers teams to make data-driven decisions. This training enhances an individual’s ability to contribute to the resolution of complex issues, leading to personal growth and professional development. Acquiring proficiency in 8D Problem Solving opens up new opportunities for individuals in their further careers.
During this 1-day 8D Problem-Solving Training Course, delegates will learn how to define problem statements, gather and analyse relevant data, identify root causes using various analytical techniques, and develop and implement corrective actions. They will also learn about documenting and reporting their findings, as well as strategies for preventing problem recurrence and driving continuous improvement. This training will be conducted by our highly professional and skilled trainer, who has years of experience in teaching.
Course Objectives
- To understand the principles and framework of 8D Problem Solving
- To implement and monitor the effectiveness of corrective actions
- To collaborate effectively within cross-functional problem-solving teams
- To document, and report findings and recommendations professionally
- To prevent problem recurrence through preventive measures
- To foster a culture of continuous improvement and learning
After attending this 8D Problem-Solving Training Course, delegates will be able to identify, define, and analyse complex problems, utilising various analytical techniques to uncover root causes.
What’s included in this 8D Problem Solving Training Course?
- World-Class Training Sessions from Experienced Instructors
- 8D Problem Solving Training Certificate
- Digital Delegate Pack
Why choose us
Ways to take this course.
Experience live, interactive learning from home with The Knowledge Academy's Online Instructor-led 8D Problem Solving Training Course. Engage directly with expert instructors, mirroring the classroom schedule for a comprehensive learning journey. Enjoy the convenience of virtual learning without compromising on the quality of interaction.
- See trainer’s screen
- Recording & transcripts
- Virtual whiteboard
- Share documents
- Works on all devices
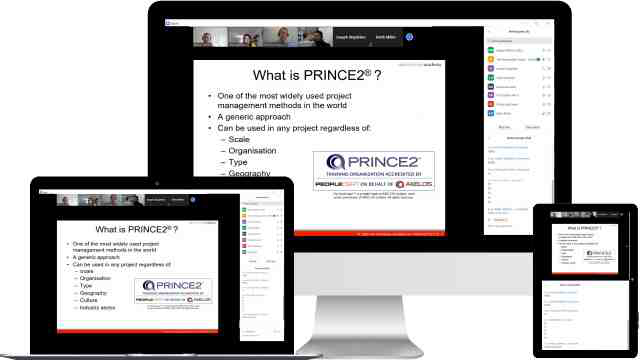
Unlock your potential with The Knowledge Academy's 8D Problem Solving Training Course, accessible anytime, anywhere on any device. Enjoy 90 days of online course access, extendable upon request, and benefit from the support of our expert trainers. Elevate your skills at your own pace with our Online Self-paced sessions.
- Certificates provided online
- Get immediate access on purchase
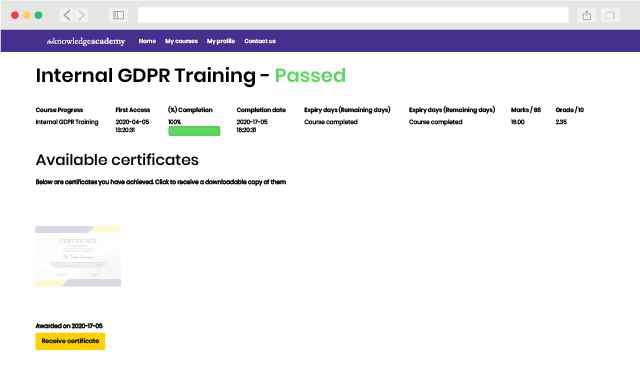
Experience the most sought-after learning style with The Knowledge Academy's 8D Problem Solving Training Course. Available in 490+ locations across 190+ countries, our hand-picked Classroom venues offer an invaluable human touch. Immerse yourself in a comprehensive, interactive experience with our expert-led 8D Problem Solving Training Course sessions.

Highly experienced trainers
Boost your skills with our expert trainers, boasting 10+ years of real-world experience, ensuring an engaging and informative training experience

State of the art training venues
We only use the highest standard of learning facilities to make sure your experience is as comfortable and distraction-free as possible

Small class sizes
Our Classroom courses with limited class sizes foster discussions and provide a personalised, interactive learning environment

Great value for money
Achieve certification without breaking the bank. Find a lower price elsewhere? We'll match it to guarantee you the best value
Streamline large-scale training requirements with The Knowledge Academy’s In-house/Onsite 8D Problem Solving Training Course at your business premises. Experience expert-led classroom learning from the comfort of your workplace and engage professional development.

Tailored learning experience
Leverage benefits offered from a certification that fits your unique business or project needs

Maximise your training budget
Cut unnecessary costs and focus your entire budget on what really matters, the training.

Team building opportunity
Our 8D Problem Solving Training Course offers a unique chance for your team to bond and engage in discussions, enriching the learning experience beyond traditional classroom settings
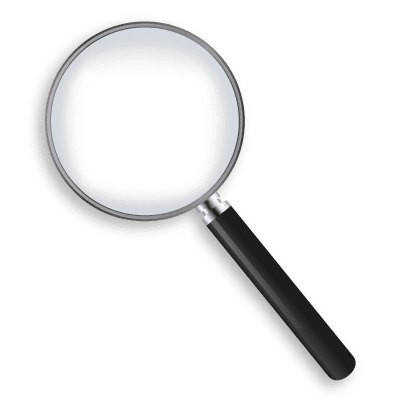
Monitor employees progress
The course know-how will help you track and evaluate your employees' progression and performance with relative ease
Some of our worldclass trainers
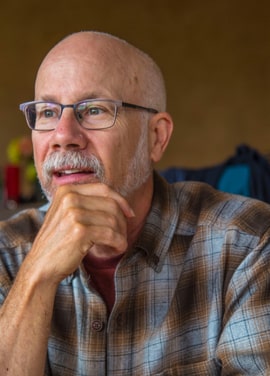
Title, job roles, etc
Retro occupy organic, stumptown shabby chic pour-over roof party DIY normcore. Actually artisan organic occupy, Wes Anderson ugh whatever pour-over gastropub selvage.
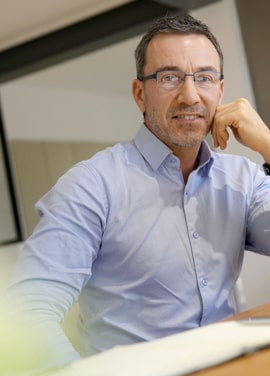
What our customers are saying
Sandra was very knowledgeable and open to discussion about subject matter in addition to course materials. This allowed the course time to flow easily and gave a greater insight to processes needed to be successful.
Mallory DuBois
8d problem solving training course faqs, what time shall i arrive at the venue, do you offer support for the course, what is included in the course, what is the duration of this course, how long until i receive the course confirmation details, what is the cost/training fees for 8d problem solving training course certification in the united kingdom, which is the best training institute/provider of 8d problem solving training course in the united kingdom, what are the best management courses courses in the united kingdom.
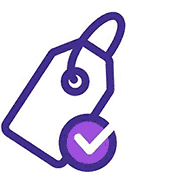
Best price in the industry
You won't find better value in the marketplace. If you do find a lower price, we will beat it.
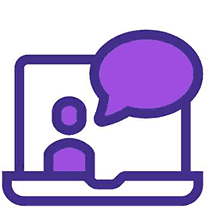
Many delivery methods
Flexible delivery methods are available depending on your learning style.
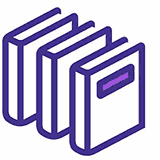
High quality resources
Resources are included for a comprehensive learning experience.

"Really good course and well organised. Trainer was great with a sense of humour - his experience allowed a free flowing course, structured to help you gain as much information & relevant experience whilst helping prepare you for the exam"
Joshua Davies, Thames Water
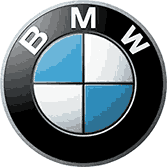
"...the trainer for this course was excellent. I would definitely recommend (and already have) this course to others."
Diane Gray, Shell
Related courses
Looking for more information on management courses, 8d problem solving training course in united kingdom.
- Upcoming classes
- Package deals
DELIVERY METHOD
SELECT AN UPCOMING CLASS View all package deals
Get a custom course package
We may not have any package deals available including this course. If you enquire or give us a call on 01344203999 and speak to our training experts, we should be able to help you with your requirements.
Limited budget?
Best price guaranteed!
OUR BIGGEST SPRING SALE!

My employer
We cannot process your enquiry without contacting you, please tick to confirm your consent to us for contacting you about your enquiry.
By submitting your details you agree to be contacted in order to respond to your enquiry.
We may not have the course you’re looking for. If you enquire or give us a call on 01344203999 and speak to our training experts, we may still be able to help with your training requirements.
Or select from our popular topics
- ITIL® Certification
- Lean Six Sigma Certification
- Scrum Certification
- Change Management Certification
- Business Analysis Courses
- Microsoft Azure Certification
- Microsoft Excel Courses
- Microsoft Project
- Explore more courses
Press esc to close
Fill out your contact details below and our training experts will be in touch.
Fill out your contact details below
WHO WILL BE FUNDING THE COURSE?
By submitting your details you agree to be contacted in order to respond to your enquiry
Thank you for your enquiry!
One of our training experts will be in touch shortly to go over your training requirements.
Back to Course Information
Fill out your contact details below so we can get in touch with you regarding your training requirements.
* WHO WILL BE FUNDING THE COURSE?
Preferred Contact Method
No preference
Back to course information
Fill out your training details below
Fill out your training details below so we have a better idea of what your training requirements are.
HOW MANY DELEGATES NEED TRAINING?
HOW DO YOU WANT THE COURSE DELIVERED?
Online Instructor-led
Online Self-paced
WHEN WOULD YOU LIKE TO TAKE THIS COURSE?
Next 2 - 4 months
WHAT IS YOUR REASON FOR ENQUIRING?
Looking for some information
Looking for a discount
I want to book but have questions
One of our training experts will be in touch shortly to go overy your training requirements.
Your privacy & cookies!
Like many websites we use cookies. We care about your data and experience, so to give you the best possible experience using our site, we store a very limited amount of your data. Continuing to use this site or clicking “Accept & close” means that you agree to our use of cookies. Learn more about our privacy policy and cookie policy cookie policy .
We use cookies that are essential for our site to work. Please visit our cookie policy for more information. To accept all cookies click 'Accept & close'.

How it works
For Business
Join Mind Tools
Article • 8 min read
8D Problem Solving Process
Solving major problems in a disciplined way.
By the Mind Tools Content Team
(Also known as Global 8D Problem Solving)
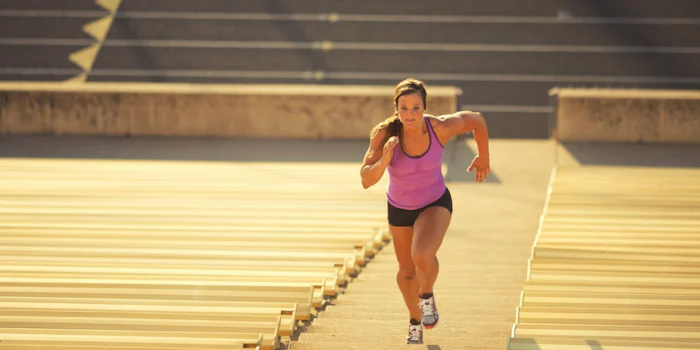
When your company runs into a major problem, you need to address it quickly. However, you also need to deal with it thoroughly and ensure that it doesn't recur – and this can take a lot of effort and elapsed time.
The 8D Problem Solving Process helps you do both of these seemingly-contradictory things, in a professional and controlled way. In this article, we'll look at the 8D Problem Solving Process, and we'll discuss how you can use it to help your team solve major problems.
Origins of the Tool
The Ford Motor Company® developed the 8D (8 Disciplines) Problem Solving Process, and published it in their 1987 manual, "Team Oriented Problem Solving (TOPS)." In the mid-90s, Ford added an additional discipline, D0: Plan. The process is now Ford's global standard, and is called Global 8D.
Ford created the 8D Process to help teams deal with quality control and safety issues; develop customized, permanent solutions to problems; and prevent problems from recurring. Although the 8D Process was initially applied in the manufacturing, engineering, and aerospace industries, it's useful and relevant in any industry.
The eight disciplines are shown in figure 1, below:
Figure 1: The 8D Problem Solving Process
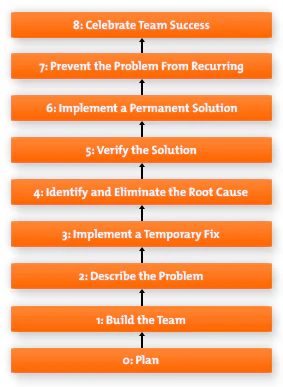
The 8D Process works best in teams tasked with solving a complex problem with identifiable symptoms. However, you can also use this process on an individual level, as well.
Applying the Tool
To use the 8D Process, address each of the disciplines listed below, in order. Take care not to skip steps, even when time is limited; the process is only effective when you follow every step.
Discipline 0: Plan
Before you begin to assemble a team to address the problem, you need to plan your approach. This means thinking about who will be on the team, what your time frame is, and what resources you'll need to address the problem at hand.
Discipline 1: Build the Team
You should aim to put together a team that has the skills needed to solve the problem, and that has the time and energy to commit to the problem solving process.
Keep in mind that a diverse team is more likely to find a creative solution than a team of people with the same outlook (although if outlooks are too diverse, people can spend so much time disagreeing that nothing gets done).
Create a team charter that outlines the team's goal and identifies each person's role. Then, do what you can to build trust and get everyone involved in the process that's about to happen.
If your team is made up of professionals who haven't worked together before, consider beginning with team-building activities to ensure that everyone is comfortable working with one another.
Discipline 2: Describe the Problem
Once your team has settled in, describe the problem in detail. Specify the who, what, when, where, why, how, and how many; and use techniques like CATWOE and the Problem-Definition Process to ensure that you're focusing on the right problem.
Start by doing a Risk Analysis – if the problem is causing serious risks, for example, to people's health or life, then you need to take appropriate action. (This may include stopping people using a product or process until the problem is resolved.)
If the problem is with a process, use a Flow Chart , Swim Lane Diagram , or Storyboard to map each step out; these tools will help your team members understand how the process works, and, later on, think about how they can best fix it.
Discovering the root cause of the problem comes later in the process, so don't spend time on this here. Right now, your goal is to look at what's going wrong and to make sure that your team understands the full extent of the problem.
Discipline 3: Implement a Temporary Fix
Once your team understands the problem, come up with a temporary fix. This is particularly important if the problem is affecting customers, reducing product quality, or slowing down work processes.
Harness the knowledge of everyone on the team. To ensure that each person's ideas are heard, consider using brainstorming techniques such as Round Robin Brainstorming or Crawford's Slip Writing Method , alongside more traditional team problem solving discussions.
Once the group has identified possible temporary fixes, address issues such as cost, implementation time, and relevancy. The short-term solution should be quick, easy to implement, and worth the effort.
Discipline 4: Identify and Eliminate the Root Cause
Once your temporary fix is in place, it's time to discover the root cause of the problem.
Conduct a Cause and Effect Analysis to identify the likely causes of the problem. This tool is useful because it helps you uncover many possible causes, and it can highlight other problems that you might not have been aware of. Next, apply Root Cause Analysis to find the root causes of the problems you've identified.
Once you identify the source of the problem, develop several permanent solutions to it.
If your team members are having trouble coming up with viable permanent solutions, use the Straw Man Concept to generate prototype solutions that you can then discuss, tear apart, and rebuild into stronger solutions.
Discipline 5: Verify the Solution
Once your team agrees on a permanent solution, make sure that you test it thoroughly before you fully implement it, in the next step.
- Conducting a Failure Mode and Effects Analysis (FMEA) to spot any potential problems.
- Using Impact Analysis to make sure that there will be no unexpected future consequences.
- Using Six Thinking Hats to examine the fix from several different emotional perspectives.
Last, conduct a Blind Spot Analysis to confirm that you and your team haven't overlooked a key factor, or made an incorrect assumption about this solution.
Discipline 6: Implement a Permanent Solution
Once your team reaches a consensus on the solution, roll your fix out. Monitor this new solution closely for an appropriate period of time to make sure that it's working correctly, and ensure that there are no unexpected side effects.
Discipline 7: Prevent the Problem From Recurring
When you're sure that the permanent solution has solved the problem, gather your team together again to identify how you'll prevent the problem from recurring in the future.
You might need to update your organization's standards, policies, procedures, or training manual to reflect the new fix. You'll likely also need to train others on the new process or standard. Finally, you'll need to consider whether to change your management practices or procedures to prevent a recurrence.
Discipline 8: Celebrate Team Success
The last step in the process is to celebrate and reward your team's success . Say "thank you" to everyone involved, and be specific about how each person's hard work has made a difference. If appropriate, plan a party or celebration to communicate your appreciation.
Before the team disbands, conduct a Post-Implementation Review to analyze whether your solution is working as you thought, and to improve the way that you solve problems in the future.
In the late 1980s, Ford Motor Company developed the 8D (8 Disciplines) Problem Solving Process to help manufacturing and engineering teams diagnose, treat, and eliminate quality problems. However, teams in any industry can use this problem solving process.
The eight disciplines are:
- Build the Team.
- Describe the Problem.
- Implement a Temporary Fix.
- Identify and Eliminate the Root Cause.
- Verify the Solution.
- Implement a Permanent Solution.
- Prevent the Problem From Recurring.
- Celebrate Team Success.
The 8D Problem Solving Process is best used with a team solving complex problems; however, individuals can also use it to solve problems on their own.
Ford is a registered trademark of the Ford Motor Company: https://www.ford.com/
You've accessed 1 of your 2 free resources.
Get unlimited access
Discover more content
Managing your boundaries at work.
Set Boundaries to Protect Your Time and Energy
Level 5 Leadership
Achieving "Greatness" as a Leader
Add comment
Comments (0)
Be the first to comment!
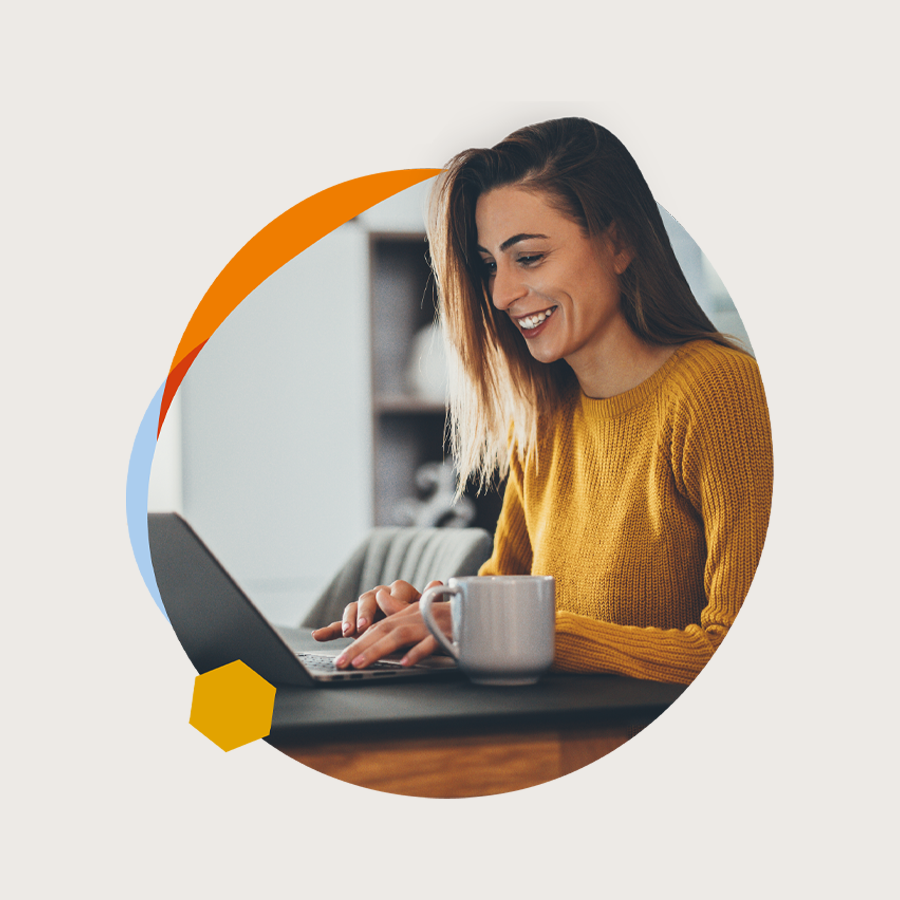
Gain essential management and leadership skills
Busy schedule? No problem. Learn anytime, anywhere.
Subscribe to unlimited access to meticulously researched, evidence-based resources.
Join today and save on an annual membership!
Sign-up to our newsletter
Subscribing to the Mind Tools newsletter will keep you up-to-date with our latest updates and newest resources.
Subscribe now
Business Skills
Personal Development
Leadership and Management
Member Extras
Most Popular
Latest Updates
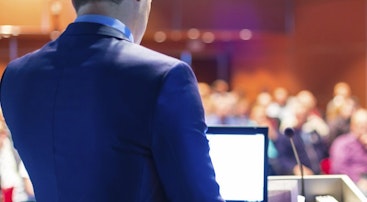
Better Public Speaking
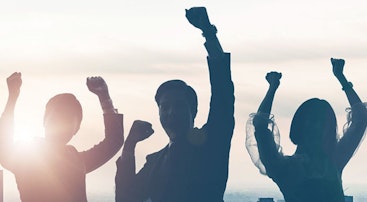
How to Build Confidence in Others
Mind Tools Store
About Mind Tools Content
Discover something new today
How to create psychological safety at work.
Speaking up without fear
How to Guides
Pain Points Podcast - Presentations Pt 1
How do you get better at presenting?
How Emotionally Intelligent Are You?
Boosting Your People Skills
Self-Assessment
What's Your Leadership Style?
Learn About the Strengths and Weaknesses of the Way You Like to Lead
Recommended for you
Value-based management.
Managing for the Long Term by Maximizing Value, Not Profit
Business Operations and Process Management
Strategy Tools
Customer Service
Business Ethics and Values
Handling Information and Data
Project Management
Knowledge Management
Self-Development and Goal Setting
Time Management
Presentation Skills
Learning Skills
Career Skills
Communication Skills
Negotiation, Persuasion and Influence
Working With Others
Difficult Conversations
Creativity Tools
Self-Management
Work-Life Balance
Stress Management and Wellbeing
Coaching and Mentoring
Change Management
Team Management
Managing Conflict
Delegation and Empowerment
Performance Management
Leadership Skills
Developing Your Team
Talent Management
Problem Solving
Decision Making
Member Podcast
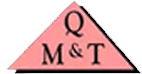
Quality Management & Training
8D PROBLEM SOLVING
8D is a recognised methodology for addressing concerns and opportunities for improvement. It is applicable to a broad range of problems, from those which are simple, to those which are rather more challenging.
It is applicable to both manufacturing and non-manufacturing activities and is utilised by a broad range of organisations and industry sectors.
Many customers require their suppliers to utilise the 8D process for the management of concerns.
BUSINESS BENEFITS
- Establishes a structured and consistent approach to problem solving within an organisation
- Enables personnel to become more effective at problem solving
- Promotes a team-based approach and engages people in ownership of problems
- Helps to ensure that customers receive a timely and effective response to concerns
- Supports the requirements of quality management systems for corrective action, problem solving, and continual improvement
- Helps to avoid future problems and reduce Cost of Poor Quality (COPQ) by exploiting the lessons learned through process improvement actions
- Assists an organisation to comply with customer-specific requirements for the management of concerns
WHO SHOULD ATTEND?
Multidisciplinary: Personnel from all functions, who lead, or are involved with, problem solving and continual improvement activities.
COURSE OBJECTIVES
The delegates should understand:
- Why it is necessary to solve problems
- The methodical 8D process for problem-solving
- The benefits of using a team approach
- How a variety of useful tools and techniques are used during 8D
- The importance of identifying the root cause(s) of a problem
- The importance of effective corrective action as a key output of 8D
- The linkage with quality management system requirements
COURSE STRUCTURE
Introduction to problem solving
Protect the customer / Initiate the 8D process
- Emergency Response Action (ERA)
- Tools and techniques for quantifying the problem (e.g. tally chart, paynter chart, measles chart, pareto chart)
Selecting a team
Describing the problem
- Process mapping / run chart / pareto matrix / histogram
Interim Containment Action (ICA)
Root cause analysis
- Comparative analysis / brainstorming / fishbone chart / 5-whys / scatter chart / tree diagram
Developing and implementing permanent corrective actions
- Tools & techniques for developing solutions / Validation activities
Preventing recurrence of the problem
- Application to other products / processes
- Process and system improvements
Completing the problem solving activity
COURSE DATES AND COST
See Training Courses for price list and order form
- Quick Links
- - 8D PROBLEM SOLVING
- - PROJECT QA
- - PROCESS MAPPING
- - POKA-YOKE
- - AS 9100 FOUNDATION
- - AS 9100 AUDIT
- - BUSINESS PROCESS ANALYSIS
- - CORE TOOLS PROGRAMME
- - CUSTOMER SATISFACTION
- - FAILURE MODE & EFFECTS
- - FAULT TREE ANALYSIS
- - ISO TS 16949 FOUNDATION
- - ISO TS 16949 AUDIT
- - ISO 9001 INTERNAL AUDIT
- - ISO 20000 FOUNDATION
- - ISO 20000 AUDIT
- - INSPECTION TECHNIQUES
- - MEASURING TECHNIQUES
- - PRINCIPLES & PRACTICES
- - ROOT CAUSE ANALYSIS
- - SIX SIGMA
- - SOFTWARE QA
- - STATISTICAL PROCESS CONTROL
- - QUALITY PLANNING
- - SUPPLIER QUALITY ASSURANCE
- - TAGUCHI TECHNIQUE
- - VALUE STREAM MAPPING
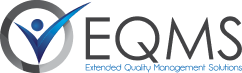
8D Problem Solving Training
Training overview.
This training provides a detailed understanding of a structured problem-solving process. Working through structured steps and using a variety of linked tools, practical examples and exercises are used in the different steps to improve the learning and understanding of the material.
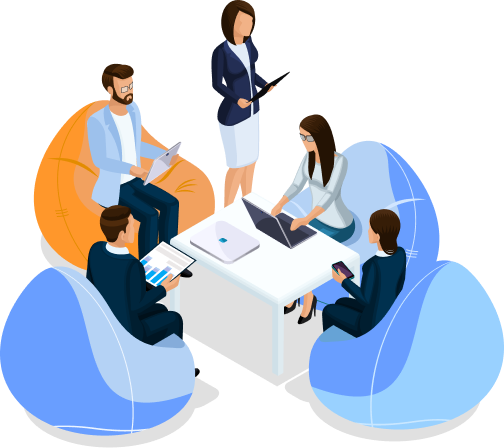
What will you learn?
During the 8D Training participants will learn to:
- Describe the benefits of using the 8D model for solving problems.
- Identify the steps of the 8D problem solving model.
- Know when to apply 8D.
- Identify which problem solving tools are best used in each step in the 8D process.
- Design a Check Sheet for recording data.
- Construct a Pareto Chart.
- Use an IS/IS NOT analysis for problem definition.
- Use the 5 Whys (Multiple Whys).
- Use Structured Brainstorming techniques.
- Create a Cause and Effect (Fishbone) Diagram.
- Create a Histogram.
- Create a Scatter Diagram.
- Describe the fundamentals of Value Stream Mapping.
- Basic principles of Statistical Process Control.
- Describe the use of Process Capability (Cp and Cpk).
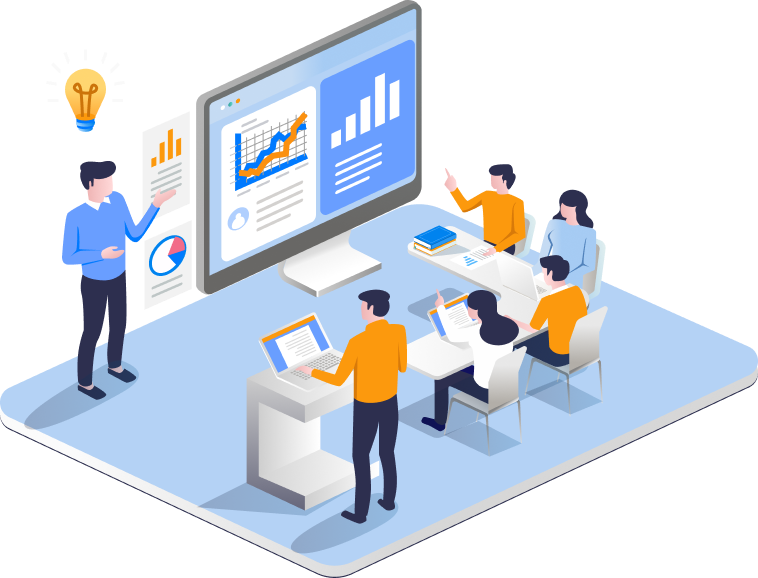
The Benefits of the 8D Problem Solving Training
- Enables personnel to become more effective at problem solving.
- Helps to establish a formal process for solving and managing problems.
Who Should Attend the 8D Problem Solving Training?
- All personnel who lead, or are involved with, problem-solving and continual improvement activities.
8D Problem Solving Training Agenda
- Introduction
- Basic introduction to 8D
- When to apply 8D
- The 8D Methodology
- Building the team
- Team members and the Roles and Resp.
- Basic Team rules
- Problem Statement
- Is/Is Not Analysis
- 5W2H Analysis
- Why/When containment action
- Commonly used Containment Action’s
- Implement and verify Containment / Interim Actions
- Data Collection
- Process Mapping
- Brainstorming
- 5 Why Analysis
- Cause and Effect Diagram
- Graphical Analysis
- Define Corrective Actions
- Selection of CA through prioritisation and risk analysis
- Implementation of Corrective Actions
- Preventive Actions
- Mistake Proofing (Poka-yoke)
- Broaden to implement at other areas/processes
- Developing employees
- Team Recognition
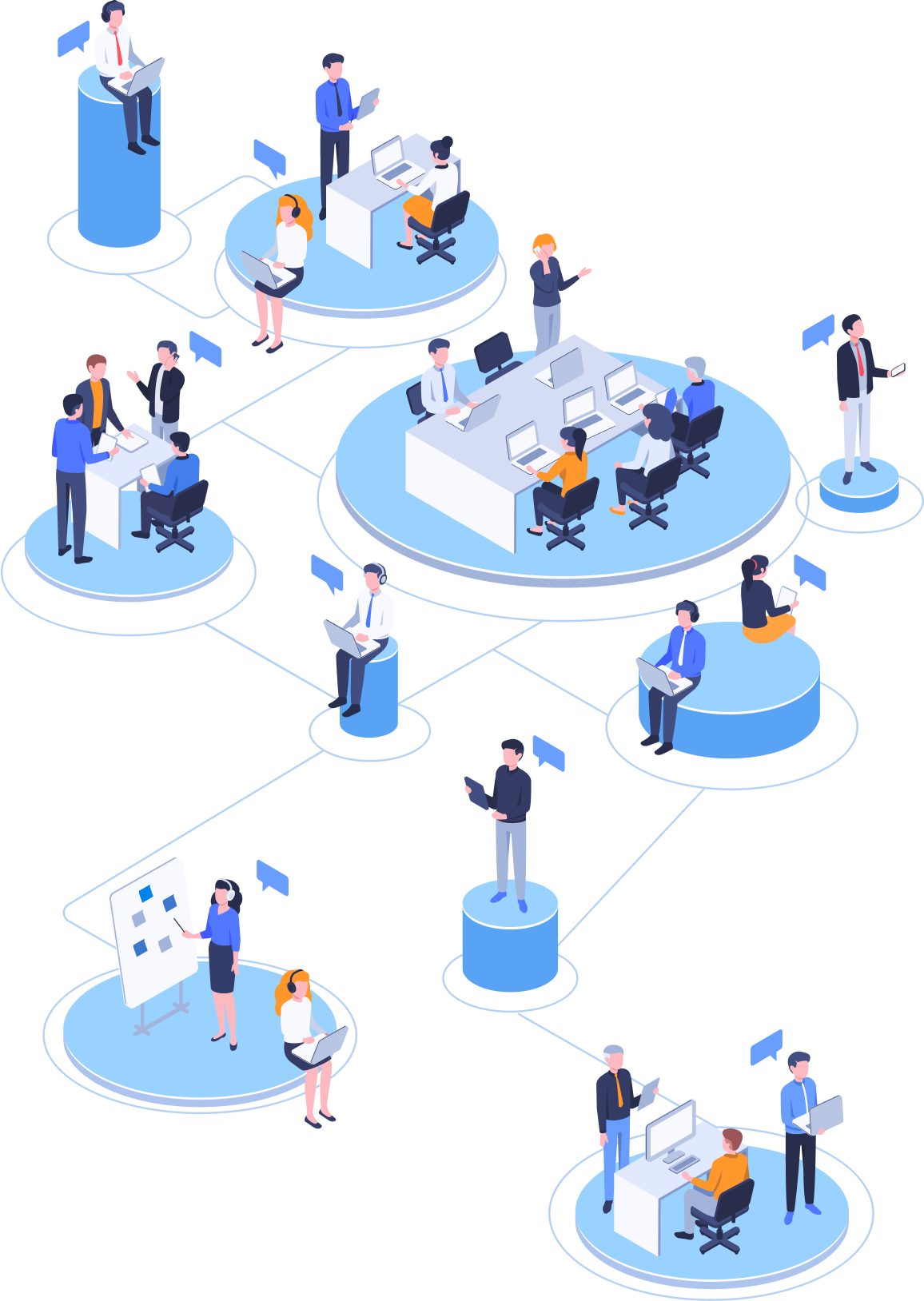
Just a Few of Our Clients
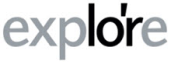
Request a Free Consultation
Contact us to discuss your needs and see how we can support to reach your goal.
- Product overview
- All features
- App integrations
CAPABILITIES
- project icon Project management
- Project views
- Custom fields
- Status updates
- goal icon Goals and reporting
- Reporting dashboards
- workflow icon Workflows and automation
- portfolio icon Resource management
- Time tracking
- my-task icon Admin and security
- Admin console
- asana-intelligence icon Asana Intelligence
- list icon Personal
- premium icon Starter
- briefcase icon Advanced
- Goal management
- Organizational planning
- Campaign management
- Creative production
- Content calendars
- Marketing strategic planning
- Resource planning
- Project intake
- Product launches
- Employee onboarding
- View all uses arrow-right icon
- Project plans
- Team goals & objectives
- Team continuity
- Meeting agenda
- View all templates arrow-right icon
- Work management resources Discover best practices, watch webinars, get insights
- What's new Learn about the latest and greatest from Asana
- Customer stories See how the world's best organizations drive work innovation with Asana
- Help Center Get lots of tips, tricks, and advice to get the most from Asana
- Asana Academy Sign up for interactive courses and webinars to learn Asana
- Developers Learn more about building apps on the Asana platform
- Community programs Connect with and learn from Asana customers around the world
- Events Find out about upcoming events near you
- Partners Learn more about our partner programs
- Support Need help? Contact the Asana support team
- Asana for nonprofits Get more information on our nonprofit discount program, and apply.
Featured Reads
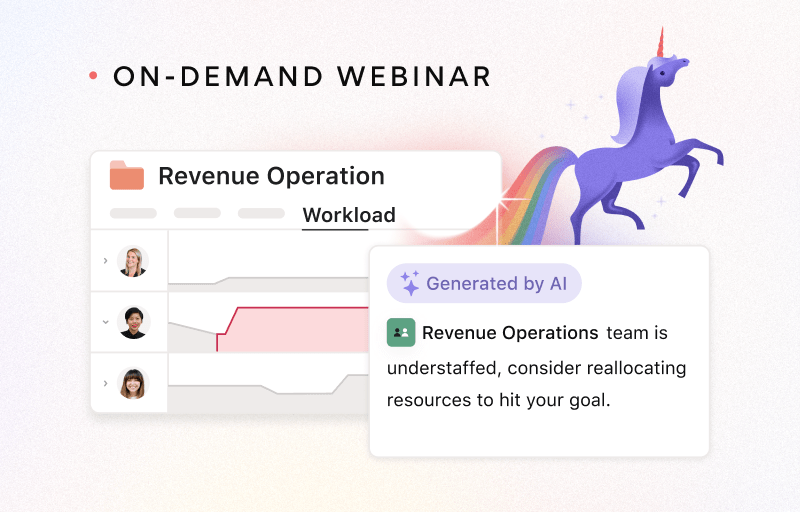
- Project management |
- What is 8D? A template for efficient pr ...
What is 8D? A template for efficient problem-solving
How you respond when problems arise is one of the most defining qualities of a manager. Luckily, there are tools you can use to master problem-solving. The 8D method of problem-solving combines teamwork and basic statistics to help you reach a logical solution and prevent new issues from arising.
You’ve spent months overseeing the development of your company's newest project. From initiation, planning, and execution, you’re confident this may be your best work yet.
Until the feedback starts rolling in.
There’s no sugar-coating it—things don’t always go as planned. But production or process issues are hardly a signal to throw in the towel. Instead, focus on honing your problem-solving skills to find a solution that keeps it from happening again.
The 8D method of problem solving emphasizes the importance of teamwork to not only solve your process woes but prevent new ones from occurring. In this guide, we’ll break down what 8D is, how to use this methodology, and the benefits it can give to you and your team. Plus, get an 8D template to make solving your issue easier.
What is 8D?
The eight disciplines (8D) method is a problem-solving approach that identifies, corrects, and eliminates recurring problems. By determining the root causes of a problem, managers can use this method to establish a permanent corrective action and prevent recurring issues.
How do you use the 8D method?
The 8D method is a proven strategy for avoiding long-term damage from recurring problems. If you’re noticing issues in your workflow or processes, then it’s a good time to give this problem-solving method a try.
To complete an 8D analysis, follow “the eight disciplines” to construct a statistical analysis of the problem and determine the best solution.
The eight disciplines of problem-solving
8D stands for the eight disciplines you will use to establish an 8D report. As you may notice, this outline starts with zero, which makes nine total disciplines. The “zero stage” was developed later as an initial planning stage.
To illustrate these steps, imagine your organization experienced a decline in team innovation and productivity this past year. Your stakeholders have noticed and want to see changes implemented within the next six months. Below, we’ll use the 8D process to uncover a morale-boosting solution.
D0: Prepare and plan
Before starting the problem-solving process, evaluate the problem you want to solve. Understanding the background of the problem will help you identify the root cause in later steps.
Collect information about how the problem has affected a process or product and what the most severe consequences may be. Planning can include:
Gathering data
Determining the prerequisites for solving the problem
Collecting feedback from others involved
If we look back at our example, you may want to figure out whether this decline in morale is organization-wide or only applies to a few departments. Consider interviewing a few employees from different departments and levels of management to gain some perspective. Next, determine what knowledge and skills you will need to solve this lapse in productivity.
D1: Form your team
Create a cross-functional team made up of people who have knowledge of the various products and workflows involved. These team members should have the skills needed to solve the problem and put corrective actions in place.
Steps in this discipline may include:
Appointing a team leader
Developing and implementing team guidelines
Determining team goals and priorities
Assigning individual roles
Arranging team-building activities
From our example, a solid team would consist of people with first-hand experience with the issues—like representatives from all departments and key people close to workshop-level work. You may also want to pull someone in from your HR department to help design and implement a solution. Most importantly, make sure the people you choose want to be involved and contribute to the solution.
D2: Identify the problem
You may have a good understanding of your problem by now, but this phase aims to break it down into clear and quantifiable terms by identifying the five W’s a and two H’s (5W2H):
Who first reported the problem?
What is the problem about?
When did it occur and how often?
Where did it occur (relating to the sector, supplier, machine, or production line involved)?
Why is solving the problem important?
How was the problem first detected?
How many parts/units/customers are affected?
Use your team’s insights to answer these questions. From our example, your team may conclude that:
Employees feel overwhelmed with their current workload.
There is no real structure or opportunity to share new ideas.
Managers have had no training for meetings or innovation settings.
Disgruntled employees know they can achieve more—and want to achieve more—even if they seem disengaged.
Once you answer these questions, record an official problem statement to describe the issue. If possible, include photos, videos, and diagrams to ensure all parties have a clear understanding of the problem. It may also help to create a flowchart of the process that includes various steps related to the problem description.
D3: Develop an interim containment plan
Much like we can expect speedy first aid after an accident, your team should take immediate actions to ensure you contain the problem—especially if the problem is related to customer safety.
An interim containment plan will provide a temporary solution to isolate the problem from customers and clients while your team works to develop a permanent corrective action. This band-aid will help keep your customers informed and safe—and your reputation intact.
Because your findings revealed workers were overworked and managers lacked training, your team suggests scheduling a few mandatory training sessions for leaders of each department covering time and stress management and combating burnout . You may also want to have a presentation outlining the topics of this training to get key managers and stakeholders interested and primed for positive upcoming changes.
D4: Verify root causes and escape points
Refer back to your findings and consult with your team about how the problem may have occurred. The root cause analysis involves mapping each potential root cause against the problem statement and its related test data. Make sure to test all potential causes—fuzzy brainstorming and sloppy analyses may cause you to overlook vital information.
In our example, focus on the “why” portion of the 5W2H. You and your team identify six root causes:
Managers have never had any training
There is a lack of trust and psychological safety
Employees don’t understand the objectives and goals
Communication is poor
Time management is poor
Employees lack confidence
In addition to identifying the root causes, try to pinpoint where you first detected the problem in the process, and why it went unnoticed. This is called the escape point, and there may be more than one.
D5: Choose permanent corrective actions
Work with your team to determine the most likely solution to remove the root cause of the problem and address the issues with the escape points. Quantitatively confirm that the selected permanent corrective action(s) (PCA) will resolve the problem for the customer.
Steps to choosing a PCA may include:
Determining if you require further expertise
Ensuring the 5W2Hs are defined correctly
Carrying out a decision analysis and risk assessment
Considering alternative measures
Collecting evidence to prove the PCA will be effective
Your team decides to roll out the training used in the interim plan to all employees, with monthly company-wide workshops on improving well-being. You also plan to implement meetings, innovation sessions, and team-coaching training for managers. Lastly, you suggest adopting software to improve communication and collaboration.
D6: Implement your corrective actions
Once all parties have agreed on a solution, the next step is to create an action plan to remove the root causes and escape points. Once the solution is in effect, you can remove your interim containment actions.
After seeing success with the training in the interim phase, your stakeholders approve all of your team’s proposed PCAs. Your representative from HR also plans to implement periodic employee wellness checks to track employee morale .
To ensure your corrective action was a success, monitor the results, customer, or employee feedback over a long period of time and take note of any negative effects. Setting up “controls” like employee wellness checks will help you validate whether your solution is working or more needs to be done.
D7: Take preventive measures
One of the main benefits of using the 8D method is the improved ability to identify necessary systematic changes to prevent future issues from occurring. Look for ways to improve your management systems, operating methods, and procedures to not only eliminate your current problem, but stop similar problems from developing later on.
Based on our example, the training your team suggested is now adopted in the new manager onboarding curriculum. Every manager now has a “meeting system” that all meetings must be guided by, and workloads and projects are managed as a team within your new collaboration software . Innovation is improving, and morale is at an all-time high!
D8: Celebrate with your team
The 8D method of problem-solving is impossible to accomplish without dedicated team members and first-class collaboration. Once notes, lessons, research, and test data are documented and saved, congratulate your teammates on a job well done! Make an effort to recognize each individual for their contribution to uncovering a successful solution.
8D report template and example
Check out our 8D report template below to help you record your findings as you navigate through the eight disciplines of problem solving. This is a formal report that can be used as a means of communication within companies, which makes for transparent problem-solving that you can apply to the entire production or process chain.
Benefits of using the 8D method
The 8D method is one of the most popular problem-solving strategies for good reason. Its strength lies in teamwork and fact-based analyses to create a culture of continuous improvement —making it one of the most effective tools for quality managers. The benefits of using the 8D method include:
Improved team-oriented problem-solving skills rather than relying on an individual to provide a solution
Increased familiarity with a problem-solving structure
A better understanding of how to use basic statistical tools for problem-solving
Open and honest communication in problem-solving discussions
Prevent future problems from occurring by identifying system weaknesses and solutions
Improved effectiveness and efficiency at problem-solving
Better collaboration = better problem solving
No matter how good a manager you are, production and process issues are inevitable. It’s how you solve them that separates the good from the great. The 8D method of problem solving allows you to not only solve the problem at hand but improve team collaboration, improve processes, and prevent future issues from arising.
Try Asana’s project management tool to break communication barriers and keep your team on track.
Related resources
What are story points? Six easy steps to estimate work in Agile
What is a flowchart? Symbols and types explained
How to choose project management software for your team
7 steps to complete a social media audit (with template)
8D Problem Solving
Introduction.
The course has been structured to give you a strategic understanding of the principles and use of 8D problem solving. A one-day course that covers the 8D problem solving techniques in context of the requirements of IATF 16949:2016. 8D problem solving is an analytical approach to investigate and identify the root cause of a concern, identify robust solutions to stop re-occurrence.
Duration: 1 Day, 09:00 – 16:00
Who Should Attend?
As the 8D problem solving techniques can form an integral part of APQP activities and become a core business continual improvement tool. This course will benefit:
- Senior Managers with responsibility for sales, design, technical, production and quality.
- Senior and line management who are responsible for creating and or implementing IATF 16949:2016 requirements.
- Engineers and technicians who can apply 8D problem solving techniques.
Course Objectives
By the end of the course delegates will understand;
- Basic 8D terminology
- Each of the 8 Disciplines
- How to complete an 8D report
- What tools and techniques to apply
Course Content
- A guide to 8D Problem Solving
- What are “the 8 disciplines”?
- How the 8 disciplines are used to drive business improvement
In-House Courses
Offering better value for money, they can be designed to closely match your specific requirements.
Style of Delivery & Course Leaders
Our course leaders have extensive experience in Quality Management across a wide range of sectors including manufacturing, service and professional organisations including Local, National and International Government. This wide experience enables them to make the course more interesting by using their relevant examples and case studies during workshop discussions. Our team of staff has extensive experience of working across cultural boundaries, through their work in Europe, Africa, Middle East, Asia and the Americas.

Certification
Delegates successfully completing the course will be awarded an IQMS registered certificate.
Booking & Course Fees
POA – This course is only available on an in-house basis, please contact us for further information.
Why train with SAI Global?
- Flexible training options: classroom , in-house , and online
- Learn from top auditing and quality practitioners
- Internationally accredited courses
In-house training for management system professionals
All our courses can be taught at your location across multiple topics, including quality management, food safety and OHS, plus specialised courses in Six Sigma and risk management.
Course Categories
- Auditor Training
- Automotive Training
- Environmental Management Training
- Food Safety Training
- Information Security Management Training
- Occupational Health & Safety Training
- Quality Management Training
- Risk Management Training
Standards & Schemes
- HACCP & TACCP
Corporate News & Resources
- SAI Global Assurance UK Home Page
- News & Resources
- Whitepapers
- Case Studies
- Scheme Notices
- Scheme Documents
SAI Global Assurance Learning
- Virtual Instructor-Led Training
- In-House Learning
- Training Venues
- Frequently Asked Questions
- Accessibility
- Terms & Conditions
- Privacy Policy
- Data Subject Requests

© 2024 SAI Global Pty Limited ABN 67 050 611 642
- ISO 9001:2015 Foundation
- ISO 14001:2015 Foundation
- ISO 45001:2018 Foundation
- Risk Management – ISO 31000:2018 Foundation
- ISO 27001:2022 Foundation
- ISO 50001:2018 Foundation
- ISO 9001:2015 Internal Auditor
- ISO 14001:2015 Internal Auditor
- ISO 45001:2018 Internal Auditor
- Internal Food Safety Auditor
- Integrated Management Systems (IMS) Internal Auditor – ISO 9001/14001:2015
- Integrated Management Systems (IMS) Internal Auditor – ISO 9001/14001:2015 & 45001:2018
- IATF 16949:2016 Internal Auditor
- BRCGS Internal Auditor
- ISO 13485:2016 Internal Auditor
- ISO 9001:2015 Lead Auditor
- IRCA ISO 14001:2015 Lead Environmental Auditor
- ISO 45001:2018 Lead Auditor
- ISO 22000:2018 Lead Auditor
- IATF 16949:2016 QMS Lead Auditor
- BRCGS Global Standard for Food Safety Issue 9 Lead Auditor
- ISO 27001:2022 Auditor Transition
- ISO 45001:2018 Auditor Migration
- ISO 22000:2018 Auditor Transition
- Design & Build a Quality Management System (QMS)
- BRCGS Global Standard for Food Safety Issue 9 Sites Training
- BRCGS Global Standard for Packaging Issue 6 – Sites Training
- BRCGS Food Safety Issue 8 – 9 Conversion Course For Auditors
- BRCGS Packaging Issue 8 – 9 Conversion for Sites
- BRCGS Global Standard for Storage & Distribution Issue 4 Sites Training
- BRCGS Global Standard for Storage & Distribution Issue 3 to 4 Conversion for Sites
- BRCGS Understanding the Requirements Agents & Brokers
- HABC Level 3 Award in Allergen Management for Catering (RQF)
- BRCGS An Approach to product safety culture
- HABC Level 3 Award in Food Safety in Manufacturing (RQF)
- HABC Level 4 Award in Food Safety in Manufacturing (RQF)
- HABC Level 2 Award in HACCP for Food Manufacturing (RQF)
- HABC Level 3 Award in HACCP for Food Manufacturing (RQF)
- HABC Level 4 Award in HACCP for Management (CODEX Principles) (RQF)
- Food Labelling & Legislation
- Microbiology for Non-Microbiologists
- Understanding & Implementing TACCP & VACCP
- BRCGS Validation & Verification
- BRCGS Risk Assessment
- BRCGS Root Cause Analysis
- Information Security
- Environmental Legislation Awareness
- Environmental Sustainability Skills for Managers
- Environmental Sustainability Skills for the Workforce
- Design & Build an Environmental Management System (EMS)
- ISO 13485:2016 Medical Devices Foundation
- ISO 13485 Internal Auditor Training
- Online Food Safety Culture for Employees
- Online Food Safety Culture for Managers
- Online Traceability Course
- Online Shelf Life Validation Course
- Online Allergens Course
- Online Cleaning & Sanitisation Course
- Online Pest Control Course
- Online Principles & Application of HACCP (Hazard Analysis Critical Control Point) Course
- Online HACCP Validation & Verification Course
- Online Introduction & Refresher to HACCP Course
- Online Implementing Foreign Body Controls Course
- Understanding Threat and Vulnerability Assessment (TACCP and VACCP)
- Online Quality Assurance & Food Safety Management Course
- Online Root Cause Analysis with 8D Course
- Online ISO 9001:2015 Foundation Course
- Online ISO 14001:2015 Foundation Course
- Online ISO/IEC 27001 Foundation
- Online ISO 31000:2018 Risk Management Course
- Online ISO 45001:2018 Foundation Course
- Virtual Training
- Online Training
- In-House Training
- Contact Sales
- Intertek SAI Global UK
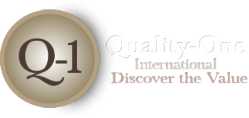
8D Training
8d training (onsite).
– Training at Your Facility –
⇓ 8D Training Course Details
⇓ 8D Training Course Description
⇓ 8D Training Course Objectives
⇓ 8D Training Course Outline
⇓ Learn More About 8D Training
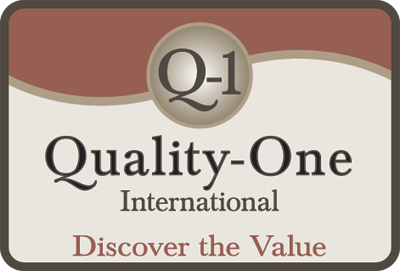
8D Course Details (Onsite)
When you choose onsite Eight Disciplines of Problem Solving (8D) Training, Quality-One brings the knowledge to you, resulting in immediate benefits for your team. The convenience of Onsite Technical Training has made it a popular option for many of our clients who require five or more participants to be trained. Expenses are minimal compared to having the whole team travel.
8D Course Description (Onsite)
The Quality-One 8D problem solving training course follows the steps of 8D in a dynamic, instructor-led environment. The course describes to participants the methodologies that have proven to be best practices for effective 8D development. Each participant will be able to interact with all of the elements of the 8D process, including the use of tools such as: Ishikawa/ Fishbone, Affinity Diagrams, Is / Is Not, Process Flow and Comparative Analysis. All activities will include industry-specific examples and terminology.
Participants will learn how to follow the 8D process steps while working in a Cross Functional Team (CFT). They will also practice problem solving tools to support a root cause and eliminate it through permanent corrective action. Participants can expect team activities and relevant exercises in a workshop format. The Quality-One 8D training materials and examples also provide an invaluable resource for review time after time.
8D Course Objectives (Onsite)
Participants can expect to learn and develop skills to confidently:
- Perform 8D step by step
- Link 8D to Failure Mode and Effects Analysis (FMEA) , Product Development Process and Advanced Product Quality Planning (APQP)
- Facilitate an effective 8D
- Participate in 8D exercises
- Define root causes and mechanisms of failure
- Set up a Cross Functional Team (CFT)
- Determine effective Interim Containment Action
- Manage and store 8D content (Lessons Learned) for future use
- Ishikawa/Fishbone
- Is / Is Not
- Statistical Process Control (SPC)
- Poka Yoke (Error Proofing)
- Understand links to Control Plan Methodology
- Complete the 8D format correctly
8D Course Outline (Onsite)
Section 1 – 8D Overview
- Team Problem Solving Principles
- Process Description (9 Step Process)
- Team Structure (Cross Functional Team)
- Inductive vs. Deductive Problem Solving
- Change-Induced Problems
- Never-Achieved Problems
Section 2 – Review of Analytical Tools in 8D
- Brainstorming Rules
- Ishikawa / Fishbone
- Affinity Diagram
- Control Chart
- Relationship between 8D and FMEA
- 5 Why (3-Legged Approach)
- Interfaces and Noise Factors
- Error Proofing
Section 3 – 8D Process Step by Step
- Problem Symptom
- Quantified Symptom
- Criteria for 8D Continuance
- Roles and Responsibilities
- Team Preparation
- Agenda and Rules
- Core Team and SMEs
- Repeated Why
- Workshop on Problem Statements and Brainstorming
- Workshop on Problem Description Development
- D3 – Interim Containment Action (ICA)
- Human Factors (Operator Error)
- Comparative Analysis
- Root Cause Theories
- Root Cause Verification
- Escape Point
- Workshop on Root Cause Theories
- Methods for Selecting PCA
- Verification of PCA
- Plan, Do, Study, Act (PDSA) Implementation Plan
- Change Management
- Stakeholders
- Validation Criteria and Sample Size
- Processes and Procedures
- Lessons Learned
- Archive of Documents
8D Training (Offsite)
– Training at Our Facility –
8D Course Details (Offsite)
8D Training in a Quality-One Technical Training Center provides participants with a learning environment that is free from interruption from daily activities. This type of course is recommended for individuals or organizations with less than 5 people who require training. Our offsite Eight Disciplines of Problem Solving (8D) Training activities are developed around principles that all participants can relate to. Offsite training also allows participants from different backgrounds and industries to share their viewpoints and experiences. This discussion often helps participants from one industry take advantage of best practices that are used in another.
8D Course Description (Offsite)
This engaging, instructor-led 8D problem solving training course takes participants through each step of the 8D problem solving process. The course offers each participant the knowledge of methodologies which have proven to be the best practices for 8D development. Each participant will be able to interact with all of the elements of the 8D process, including the use of tools such as: Ishikawa / Fishbone, Affinity Diagrams, Is / Is Not, Process Flow and Comparative Analysis.
Participants will learn how to follow the 8D process steps while working in a Cross Functional Team (CFT). They will also practice problem solving tools to support a root cause and eliminate it through permanent corrective action. Participants can expect team activities and relevant exercises in a workshop format. The Quality-One reference materials and examples also provide an invaluable resource for review time after time.
8D Course Objectives (Offsite)
8d course outline (offsite).
- Ishakawa / Fishbone
- 5 Why (3-Legged 5 Why Approach)
- D0 – Prepare (Plan) for the 8D
8D Training (Online)
– Technical Training Overview –
8D Course Details (Online)
The Quality-One Online Eight Disciplines of Problem Solving (8D) Training Overview is an excellent introduction to the 8D methodology. The course is completely interactive, featuring audio, video, animation and downloadable reference materials. Online training gives you immediate access to 8D process content and is available 24 hours a day.
8D Course Description (Online)
Quality-One Online 8D Training Overview introduces participants to the basic principles of 8D, including each step required in the 8D format. Participants will also be able to understand the sequence of the 8D process and receive guidance on what tools are involved with each step. This course follows a structured approach for defining problems and identifying root causes. The participant will have 30 days to complete this course and can access it at any time.
8D Course Objectives (Online)
Upon completion of this overview, the participant will acquire the knowledge to:
- Understand the 8D process and describe each step
- Describe the tools and methods used in support of 8D
- Explain how 8D teams are structured
- Identify Symptoms, Problem Statements, Problem Descriptions, Possible Causes, Most Likely Causes and Root Causes
- Describe Interim Containment and Permanent Corrective Actions
- Explain how Preventative Analysis benefits organizations
- Explain verification vs. validation during problem solving
- Explain how the escape points link to control plans
8D Course Outline (Online)
- Change Induced Problems
- Never Achieved Problems
- Ishakawa Fishbone
- 5 Why (3-legged Approach)
- D3 – Interim Containment Action
- Root Cause theories
- PDSA Implementation Plan
- D8 – Closure and Congratulate the Team
Learn More About 8D Training
Quality-One offers Quality and Reliability Support for Product and Process Development through Consulting, Training and Project Support. Quality-One provides Knowledge, Guidance and Direction in Quality and Reliability activities, tailored to your unique wants, needs and desires. Let us help you Discover the Value of 8D Consulting , 8D Training or 8D Project Support .
Contact Us | Discover the Value!
(248) 280-4800 | [email protected]
Remember Me
- Don't have an account? Register
- Lost your password? Click here
- Already have an account? Log in

0800 9555 798
+44 1928 716 903

- Buy Chemicals Online
What Is The 8D Problem Solving Process?
- Posted on October 7, 2020
- by Lucy Bell-Young
Back in 1983, Ford Motor Company was struggling to cope with the influx of complaints about the quality of American cars, so they decided to approach Dr W. Edwards Deming for his professional advice. Ford had expected Deming’s seminars to revolve around how to improve quality, but instead he focused on how Ford should improve management and thus, the 8D model was created as a problem-solving strategy.
In this post:
The 8D Problem Solving Format
The 8D Model, also known as the 8D Report, consists of 8 stages, or “disciplines,” that can be used to analyse problems encountered in the workplace. The main aim of the process is to identify the root cause of a problem and put procedures in place to rectify it, ensuring that the matter won’t come back to haunt you.
When managers of companies are faced with a problem, they want to solve it quickly and thoroughly. However, these terms almost contradict each other, and a quick-fix can often lead to a recurring issue. To help teams develop a customised, permanent solution to their problems, Ford published the 8 Disciplines Model in their 1987 manual for ‘Team Oriented Problem Solving’ (TOPS), and this article will show you how it works.

Discipline 0: Plan
The 8D Model should technically be renamed the 9D Model because discipline 0 was added later on as a preliminary preparation stage. The planning discipline includes pondering who will be on your team, how long you have to fix the problem, and what resources you’re likely to need in the process.
Discipline 1: Build The Team
Time to recruit some team members. This can be a puzzling decision; a diverse team may be advantageous because they can offer different skills and suggestions, but if their ideas oppose each other’s too much, you could be faced with lots of time spent solving their disagreements.
It may be good to glue the team together and encourage team work with some ice breakers and team building activities at this stage.
Discipline 2: Describe The Problem
Ensure the assembled team are filled in with a detailed background – who, what, when, where, why and how? Quantify where possible, to inform your team of the severity of the problem.
Identifying the root cause comes later on. For now, just focus on making sure your team understands what’s going on above the surface.
Discipline 3: Implement A Temporary Fix
Apply a temporary band aid to stop the problem spiralling while you figure out your next move. Get each member of the team to contribute their initial ideas and consider cost, relevancy and implementation time, making sure the procedure is worth the effort.
Discipline 4: Identify And Eliminate The Root Cause
This is where you attempt to dig out the origin. Conduct a cause-and-effect analysis using a fishbone diagram to help you uncover numerous possible causes and highlight any problems you may not have been aware of.
Apply root cause analysis to zone in on the deeper causes of the issues you’ve identified. One way to perform a root cause analysis is by asking the 5 Whys . You can then make a start on figuring out some permanent solutions to the problems.

Discipline 5: Verify The Solution
You need to test your solution before it can be fully implemented to avoid the risk of unwanted side effects. The “Six Thinking Hats” may sound like some magical objects from a Harry Potter book, but they can be a useful technique for examining your potential solution from multiple angles.
Discipline 6: Implement A Permanent Fix
Now your solution is ready to be unleashed and monitored. Make sure it’s working properly and keep an eye out for side effects.
If it doesn’t seem to be working, re-trace your steps and make any necessary modifications.
Discipline 7: Prevent The Problem From Recurring
When you’re certain you’ve found the solution, gather your team to come up with a way to prevent the problem from arising again in the future. This could involve updating your company’s policies or procedures, or training others on the new process or standard.
Discipline 8: Celebrate Your Success
Show your team you appreciate all of their hard work by thanking them all individually for their efforts and specific input. Share your developments with the rest of your employees and keep them informed of the new way of working and problem-solving.
At ReAgent, we like to gather a team and progress through the 8D model whenever we encounter any major problems. To illustrate, here’s an example of a hypothetical issue that could well occur in our factory:

When To Use 8D Problem Solving
Since 8D was created to ensure that best practices are applied to problem solving, it should be used whenever a recurring or serious issue pops up. 8D problem solving is typically used when the following have been discovered:
- Safety or regulatory issues
- Frequent equipment test failures
- Poor performance or productivity
- Unprecedented numbers of complaints
This doesn’t mean that the 8D Model should be used for every problem, however, since this would be unnecessary and, in some cases, wasteful. This is because time spent reporting every small problem ultimately reduces productivity and wastes resources. Rather, the seriousness of an issue should be assessed prior to implementing 8D problem solving. In a nutshell, if you need to investigate the root cause of a persistent or deep-set problem, only then should the 8D Model be used.
When implementing the 8D problem solving process, using a template is key to comprehensively documenting your progress at each stage. Now that we’re in 2020, these templates are more efficient than ever, allowing you to do things like add evidence photos with annotations and make use of data analysis. 8D templates can usually be downloaded for free , giving you no excuse to continue avoiding that nagging problem!
All content published on the ReAgent.co.uk blog is for information only. The blog, its authors, and affiliates cannot be held responsible for any accident, injury or damage caused in part or directly from using the information provided. Additionally, we do not recommend using any chemical without reading the Material Safety Data Sheet (MSDS), which can be obtained from the manufacturer. You should also follow any safety advice and precautions listed on the product label. If you have health and safety related questions, visit HSE.gov.uk .
You might also be interested in...

An ISO 9001 audit is a process that measures whether an organisation has the basic qualifications required to be certified under ISO’s quality management standards (QMS). As the name suggests, the ISO 9001 audit process primarily focuses on examining an

Selling chemicals is a highly regulated activity and it’s not without its risks. We minimise risks by only selling to established businesses, but we still need to provide the appropriate documentation with chemical sales. Some pieces of documentation are a

As you know, ReAgent have been moving closer and closer towards achieving a new accreditation: the ISO 13485 Medical Devices Standard. This will not only be testament to our quality-driven mind-set, it will also improve and expand the services we

Environmental sustainability isn’t a mere fad or legal obligation, but a logical, moral, and practical approach to doing business on a large scale. It’s all about balancing productivity, based on a company’s need to be profitable, with the environmental impact
How can ReAgent help you?

“All enquiries are treated as confidential – we never share your details” Kerry Customer Service
“Our manufacturing facility is accredited to ISO 9001, ISO 13485, ISO 14001 and ISO 45001” Darren Sales Director

“We provide comprehensive technical support with every enquiry” Jo Account Director
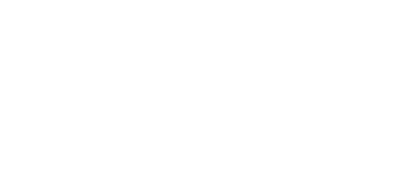
- Technical Support
- Supply Chain Management
- Why Choose ReAgent?
- Ampoule Filling
- Biological Buffers
- Chemical Mixing
- Chemical Solutions
- Chemical Bottling
- Textile Coatings
- Chemical Repacking
- Cleaning Chemical Manufacturing
- Contract Manufacturing
- Contract Packing
- Diagnostic Reagents
- Case Studies

Global 8D Training Courses G8D, UK Problem Solving
00 44 (0)1904 890 160 Get in Touch
You carry out 'Root Cause Analysis (RCA)' to permanently eliminate problems.
- Global 8D (G8D) Problem Solving Training & Consultancy
Global 8D Training
Global 8D (G8D) problem solving training and consultancy uses ‘Root Cause Analysis (RCA)’ in developing permanent corrective actions for problems. Our course has assisted clients in meeting the NADCAP ‘Root Cause Corrective Action (RCCA)’ training requirements.
The course takes a tutor led learning-though-doing workshop approach and can be delivered over 1 or 2 days with the 2 day course allowing more time for using the tools to work through some of your real process problems. We have public, virtual and in-house training course options.
Your Trainer
Kevin holds a ‘BSc Engineering Product Design’, ‘MSc Manufacturing, Management & Technology’ and ‘Level 3 Award in Education and Training’ which certifies his competence as a trainer. He is also a ‘Certified Lean Six Sigma Master Black Belt’. He was trained in 8D whilst working for Ford Motor Company and has over 13 years of experience in delivering 8D training for Claudius Consulting . Kevin brings a core philosophy of ‘learning-through-doing’ to all the programmes he designs and delivers and has developed the ability to communicate the language of ‘Global 8D’ in simple terms.
Contact us for further information or a no obligations discussion on Global 8D Problem Solving options
Training & Consultancy
Testimonials.
The practical training and guidance provided by Claudius Consulting allowed me to confidently apply the lean six sigma tools to my project.
Liang Zong, Knowledge Transfer Partnership Associate
e: [email protected] | t: 0844 884 5224
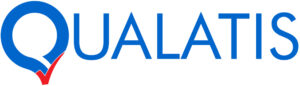
- Understanding IATF 16949
- IATF 16949 Internal Auditor
- IATF 16949 Advanced Auditor
- IATF 16949 Lead Auditor
8D Problem Solving
- FMEA – AIAG/VDA
- ISO 9001 Foundation
- Quality Internal Auditor
- ISO 9001 Lead Auditor
- About Qualatis

8D problem solving is an 8 step process for to investigate and identify the root cause of a concern, identify robust solutions to stop re-occurrence. Whilst this problem solving methodology has been developed by the automotive sector it is also widely used outside of the automotive sector too.
The course utilises case studies so that delegates can solve a problem during the course. The case studies are an oil leak problem on a car or a non-automotive leaking board marker pen.
- D0 - Planning and Emergency Containment Actions
- D1 – Establish the Team
- D2 - Define the Problem
- D3 - Interim Containment Actions
- D4 - Root Causes
- D5 - Select the Permanent Corrective Actions
- D6 - Implement Permanent Corrective Actions
- D7 - Preventive Actions
- D8 - Team Recognise and Closure
As the 8D problem solving techniques can form an integral part of APQP activities and become a core business continual improvement tool. This course will benefit:
Senior Managers with responsibility for sales, design, technical, production and quality. Senior and line management who are responsible for creating and or implementing IATF 16949 requirements. Engineers and technicians who can apply 8D and root cause problem solving techniques.
- The 8D concept
- Applying 8D techniques
- Benefits of 8D techniques
- Applying 8D principles
- Utilising 8D solutions
- Links with Product Realisation and APQP
- 8D investigative analysis
- Effective use of problem solving
- Adapting concepts for everyday activities
Duration - 1 day / 2 days
A 2 day course will enable the 8D process to be applied to the organisation's own/live problems.
In company and online delivery.
When solving problems, dig at the roots instead of just hacking at the leaves. Anthony J. D'Angelo
Browser out of date.
It appears you're running on a very old web browser that we're unable to support. If you would like to view the site you'll need to update your browser. Please choose from any of the following modern browsers. Thanks!

Google Chrome

Mozilla Firefox

Internet Explorer
By Use Cases
By Industry
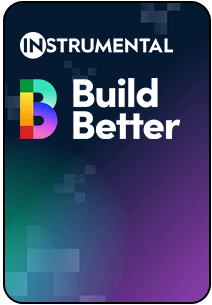
BUILD BETTER HANDBOOK
A place for visionaries to learn from their peers about getting culture right , NPI , Production , and evaluating new technologies
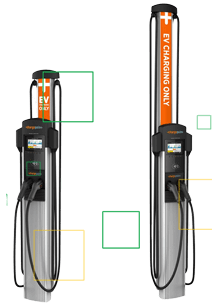
Case studies
See how companies are using Instrumental
ABOUT INSTRUMENTAL
- Log in SPEAK TO AN EXPERT
News, Blog, & Resources
Case studies, introduction to the build better handbook, manufacturing term glossary, getting culture right, jeff lutz: team culture drives product performance, scrappy ways to execute like apple, building a culture of quality, building the world's most reliable products: insights from medical and defense leaders, fear management, npi: a how to guide for engineers & their leaders, leading from the front, marcel tremblay: the olympic mindset & engineering leadership, anurag gupta: framework to accelerate npi, kyle wiens on why design repairability is good for business, nathan ackerman on npi: do the hard thing first, jdm operational excellence in npi, building the team, quality is set in development & maintained in production, 3 lessons from tesla’s former npi leader, maik duwensee: the future of hardware integrity & reliability, reject fake npi schedules to ship on time, leadership guidance for failure to meet exit criteria, screws & glue: getting stuff done, choosing the best cad software for product design, screws vs glues in design, assembly, & repair, best practices for glue in electronics, a practical guide to magnets, inspection 101: measurements, a primer on color matching, ok2fly checklists, developing your reliability test suite, guide to does (design of experiments), ten chinese phrases for your next build, npi processes & workflows, evt, dvt, pvt stage gate definitions, hardware schedules are driven by iteration, the shedletsky test: 12 requirements for npi programs, 4 best practices for generational knowledge building, production: a primer for operations, quality, & their leaders, leading for scale, greg reichow’s manufacturing process performance quadrants, 8d problem solving: sam bowen describes the power of stopping, cut costs by getting your engineers in the field, garrett bastable on building your own factory, oracle supply chain leader mitigates risk with better relationships, brendan green on working with manufacturers, surviving disaster: a lesson in quality from marcy alstott, serialization for electronics manufacturing, tactics to derisk ramp, e-commerce ratings make product quality a competitive edge, production processes & workflows, failure analysis methods for product design engineers: finding sources of error, how to improve first pass yield with instrumental, how to identify dark yield, thinking ahead: how to evaluate new technologies, build vs buy: a guide to implementing smart manufacturing technology, leonel leal on how engineers should frame a business case for innovation, saw through the buzzwords, aoi, smart aoi, & beyond: keyence vs cognex vs instrumental, visual inspection ai: aws lookout, landing ai, & instrumental, manual inspection vs. ai inspection with instrumental, electronics assembly automation tipping points, cto of asus: systems integrators for manufacturing automation don't scale, roi-driven business cases & realized value, building a buying committee, how to buy software (for those who usually don't).
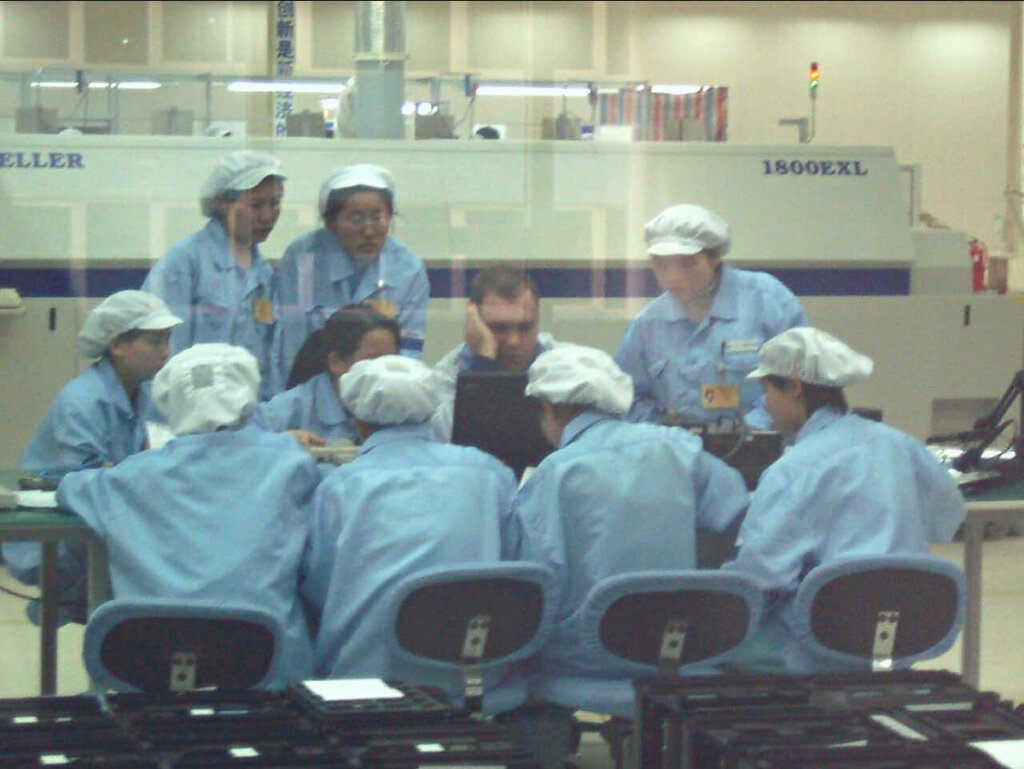
Sam Bowen with an engineering team in Tsingtao, China in 2001. He was on site for six weeks to start up the EVT line for a UK-based cellphone developer.
Sam Bowen (center) with an engineering team in Tsingtao, China in 2001. He was onsite for six weeks to start up the EVT line for a UK-based cellphone developer.
Manufacturing has countless operational frameworks. From the Five Whys to Six Sigma to 8D problem solving, each team has adopted their favorites, and each team adds their own touch — and in the process, many teams accidentally introduce or eliminate steps that create more chaos than calm.
Sound familiar? It does to Sam Bowen. Sam’s career has taken him to Amazon, Fitbit, Tonal, and Peloton, where he’s worked as a hardware development leader to build industry-defining consumer products and nurture strong manufacturing teams. He grew the Amazon hardware team from 5 to 80 people, Fitbit from 15 to 250, and Peloton from 50 to 250. He knows how to scale and how to do it methodically.
While building these teams from the ground up, he developed a deep appreciation for problem-solving and adopted 8D as his model. We sat down with Sam to learn about his team-building experiences and how he has leveraged 8D to build teams of highly methodical problem-solvers.
What is 8D problem-solving?
The 8D approach is a problem-solving methodology that follows eight disciplines to help teams identify, correct and eliminate recurring issues in manufacturing.

It looks intuitive at first glance: you plan your approach, describe and contain the problem, verify the root cause, and take specific actions until it’s resolved. But because it’s deceptively simple, Sam finds that it’s easily dismissed, and many teams incorrectly think they’re already following those steps.
Where’s the disconnect? He’s found one common thread with the most challenging steps for teams to implement: those that require a “stop.”
Stop your people: Create a team
The first steps in the 8D problem solving model is to create a plan to solve the problem, including identifying the right people. Sam believes that the simple act of stopping and assessing who is needed on a problem-solving team is critical and often overlooked.
In fact, Sam has watched disasters happen because even within one company, each team takes a different approach: when a failure is identified, the manufacturing team might start adjusting processes, or the engineering team might dive into CAD to experiment with design changes. Both teams then think they’re making progress when in reality, there’s no structure or communication around the problem they’re trying to solve in the first place.
While these communication problems are frustrating, they’re also completely understandable to Sam. He knows that each team has different success metrics and approaches problem-solving with their own bias. If you’ve been battling adhesive issues on a PCB, you may think that’s causing the failure. Or, if you had concerns about a component from an upstream supplier, you may think that component holds the answer. And while he understands the source of team confusion, he also recognizes the costly ripple effects.
“No matter the reasons, failure to communicate creates a big mess,” Sam said. “That’s why this first step to create a plan is so powerful. It causes everyone to stop and define the team before problem-solving occurs.”
Stop the line: Define containment
Despite the differences between engineering and operations teams, everyone in manufacturing agrees on one thing: do whatever it takes to avoid stopping the line. Stopping the line impacts shipment schedules and reduces product margins. Worst of all, a stopped line may be difficult to start again, because operators with experience on that program might have been reassigned elsewhere. Since everyone is hardwired to avoid stopping the line, deciding when it is necessary is especially challenging. That’s where discipline three in 8D problem solving comes in: define the containment plan.
Sam says it can be easy to jump to failure analysis early on, but containing the problem will ensure the customer is protected from a range of product issues, from defective to safety-critical.
Using 8D to stop the line at Peloton
Sam Bowen makes the call to stop the line about once a quarter. It’s never easy, and it has taken time to build trust with his team members that he was making the right call. In one particularly memorable experience early on at Peloton, his team discovered the pedals on the Bike Plus weren’t performing properly under certain mechanical tolerance tests. But the bikes were already in mass production.
“I approached the operations team and delivered the bad news that we had to stop the line — we couldn’t use the pedal, and we had to return to the old pedal,” Sam said. “I knew it meant shipment wasn’t going to happen on time, but we needed to do it.”
While Sam might have been ready to stop the line to contain the problem, the operations team wasn’t. They didn’t pivot until a month later when more data came in that proved it in fact needed to be changed. At that point, it was a scramble to order and release the replacements to production.
“It all ended up working out, and our team grew together out of that experience, but it could have gone very differently if we had stopped the line sooner.”
Stop the problem from repeating: Take preventative measures
The seventh discipline in 8D problem solving is “take preventative measures,” where teams change the operation systems and procedures to prevent the problem from happening again. This is where leaders can define their problem-solving culture — because culture doesn’t develop when you’re fighting the fire, but after the fire is put out and teams have room to assess what went well and what went wrong.
Sam tackles this discipline with retrospectives. In most retrospectives, everyone trudges to the meetings expecting finger-pointing, and in many cases, that’s exactly what happens (if a retrospective happens at all). He sees a better way to do it.
“The main challenge with retrospectives is that the problem isn’t clearly defined,” Sam said. “Do we look at the schedule, the product, the cost? It’s too broad. The biggest thing you can do to improve your retrospective is to frame the problem.”
It’s important to frame it around a problem that’s different from the one identified in step two. For example, while step two might explore why a unit is failing a drop test, step seven should be broader: why did the project launch three months late, or why did the program not meet cost targets? Identifying one question anchors the retrospective so team members rally instead of pointing fingers.
8D problem-solving protects the customer
Manufacturing teams don’t have to live with chaos. It’s a lesson Sam learned early in his career from Jeff Cantlebary, operations manager at Amazon (now at Snap). Sam saw Jeff bring order and calm to countless challenges while working together, using 8D problem-solving as a foundation. He also credits Jeff for teaching him another valuable lesson on the relationship between manufacturing leaders and customers.
“Jeff is a very smart, thoughtful person, and he brought everything back to one goal: protect the customer. Once I saw how powerful that was and how 8D helped me do that, I was all in,” Sam said. “It’s worth the time investment to stop, slow down and be intentional about problem-solving so you can both protect your customers and deliver meaningful customer experiences.”
Lean Six Sigma Training Certification

- Facebook Instagram Twitter LinkedIn YouTube
- (877) 497-4462
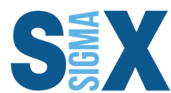
8D Corrective Action: Mastering Problem-Solving for Continuous Improvement
May 13th, 2024
Businesses constantly refine products, services, and workflows to stay ahead. But issues can still pop up, angering customers and jacking costs while hurting a company’s image. This is where the 8D corrective action problem-solving method earns its stripes.
It was developed by Ford in the 80s and has since spread widely across manufacturing, healthcare, aerospace, and more.
The 8D approach is a methodical process combining pros from different parts of the company, analytical tools, and fact-based decision-making.
By following its eight systematic steps, organizations can expertly handle thorny problems. They uncover root causes and implement lasting fixes addressing immediate concerns while fueling constant upgrades to prevent repeat issues.
Key Highlights
- Understanding the origins and history of the 8D corrective action methodology, its benefits, and when to apply it for optimal results.
- Exploring the eight disciplined steps of the 8D corrective action process.
- Integrating the 8D methodology with quality management systems, leveraging Enterprise Quality Management Software (EQMS) to streamline workflows.
- Examining case studies and examples from various industries, including manufacturing, service, healthcare, and the automotive sector.
Understanding the 8D Corrective Action Problem-Solving Methodology
The Eight Disciplines (8D) methodology is a structured, team-based approach to problem-solving that aims to identify the root causes of issues and implement effective corrective actions.
It is a comprehensive framework that combines analytical tools, cross-functional collaboration, and a disciplined mindset to tackle complex problems systematically.
The 8D process establishes a step-by-step approach that guides organizations through eight distinct disciplines, each building upon the previous one.
Origins and History of 8D Corrective Action
The origins of the 8D methodology can be traced back to the 1980s when it was developed and pioneered by Ford Motor Company.
Initially referred to as “ Team Oriented Problem Solving ” (TOPS), this approach was designed to address the recurring quality issues that plagued the automotive industry at the time.
Recognizing the limitations of traditional problem-solving techniques, Ford sought to establish a more robust and effective framework that would not only resolve immediate concerns but also drive continuous improvement and prevent future issues.
The 8D methodology quickly gained traction within Ford and was subsequently adopted as the company’s primary approach for documenting and addressing problem-solving efforts.
As the benefits of the 8D corrective action process became evident, it rapidly gained popularity among other manufacturers and industries, transcending its automotive roots.
Today, the 8D methodology is widely employed across various sectors, including manufacturing, healthcare, aerospace, and service industries, among others.
Benefits of Using 8D Corrective Action
Implementing the 8D problem-solving methodology offers numerous benefits to organizations, including:
1. Systematic Approach : The structured nature of the 8D process ensures a consistent and comprehensive approach to problem-solving, reducing the risk of overlooking critical factors or jumping to premature conclusions.
2. Root Cause Identification : By emphasizing root cause analysis , the 8D methodology goes beyond addressing surface-level symptoms and focuses on identifying and eliminating the underlying causes of problems.
3. Cross-Functional Collaboration : The team-based approach fosters cross-functional collaboration, leveraging diverse perspectives and expertise from various departments, leading to more robust and well-rounded solutions.
4. Preventive Measures : The 8D corrective action process incorporates preventive actions to mitigate the recurrence of similar issues, promoting a culture of continuous improvement and proactive problem-solving.
5. Improved Quality and Reliability : By addressing root causes and implementing corrective actions, organizations can enhance the quality and reliability of their products, services, and processes, leading to increased customer satisfaction and cost savings.
6. Knowledge Sharing and Organizational Learning : The documentation and archiving of 8D processes facilitate knowledge sharing and organizational learning, enabling teams to build upon past experiences and lessons learned.
When to Apply 8D Corrective Action
The 8D problem-solving methodology is particularly valuable in situations where:
- Root Cause Analysis is Required: When issues persist despite initial troubleshooting efforts, or when the underlying causes are not immediately apparent, the 8D process can provide a structured approach to root cause analysis.
- Recurring Problems: If an organization experiences recurring problems or quality issues, the 8D methodology can help identify and eliminate the root causes, preventing future occurrences.
- Quality Issues with Significant Impact: When quality issues have a substantial impact on customer satisfaction, safety, regulatory compliance, or financial performance, the rigorous 8D approach can be employed to address the problem comprehensively.
- Complex Problems: For intricate problems involving multiple factors, processes, or departments, the cross-functional nature of the 8D team and the systematic approach can facilitate a thorough investigation and effective solution development.
By understanding the core principles, benefits, and appropriate application scenarios of the 8D problem-solving methodology, organizations can leverage this powerful framework to drive continuous improvement , enhance quality, and maintain a competitive edge in their respective industries.
The Eight Disciplines (8D) Process
At the heart of the 8D corrective action methodology lies a structured, step-by-step approach that guides organizations through eight distinct disciplines.
Each discipline builds upon the previous one, ensuring a thorough investigation, analysis, and resolution of the problem at hand.
The eight disciplines of the 8D process are designed to facilitate a systematic and disciplined approach to problem-solving, leveraging cross-functional collaboration, analytical tools, and data-driven decision-making.
D0: Planning and Preparation
Before embarking on the 8D corrective action journey, proper planning and preparation are crucial. This initial step, often referred to as Discipline Zero (D0), lays the foundation for a successful problem-solving effort.
During D0, the team gathers relevant information about the problem, assesses the need for interim containment actions, and establishes the prerequisites for forming an effective cross-functional team.
This stage involves collecting data on symptoms, identifying potential risks, and ensuring that the necessary resources and support are in place to execute the 8D process effectively.
D1: Team Formation
The first formal discipline of the 8D process focuses on assembling a cross-functional team with the collective knowledge, skills, and expertise required to tackle the problem at hand.
Effective team formation is critical to the success of the 8D corrective action effort, as it ensures diverse perspectives and a comprehensive understanding of the issue.
During D1, team members are carefully selected from various departments or functions, such as product engineering, process engineering, quality assurance, and data analysis.
Best practices in team formation involve considering factors such as technical expertise, problem-solving skills, interpersonal abilities, and the availability and commitment of potential team members.
Establishing ground rules, communication protocols, and team-building exercises can further enhance collaboration and effective teamwork.
D2: Problem Description
In Discipline 2, the team focuses on accurately describing the problem, utilizing quantitative data and evidence-based approaches.
This step is crucial, as it establishes a shared understanding of the issue and guides the subsequent steps of the 8D process.
The problem description involves defining the problem statement in specific, measurable terms, identifying the affected product or process, and quantifying the impact on operations, quality, customer satisfaction, and costs.
Tools such as the “ 5 Whys ” technique, Ishikawa (fishbone) diagrams , and “ Is/Is Not ” analysis can aid in this process, helping to capture relevant details and categorize information.
D3: Interim Containment Actions
While the team works towards identifying and implementing permanent solutions, Discipline 3 focuses on implementing interim containment actions to mitigate the immediate impact of the problem and protect customers from further exposure.
Interim containment actions are temporary measures designed to isolate the problem and prevent it from causing further harm or spreading to other areas, processes, or products.
These actions may include segregating defective products, implementing additional inspections or checks, or introducing manual oversight until permanent corrective actions are in place.
It is essential to verify the effectiveness of interim containment actions and monitor their implementation to ensure that they are successful in containing the problem and minimizing its impact on operations and customers.
D4: Root Cause Analysis
At the core of the 8D corrective action process lies Discipline 4, which focuses on identifying the root causes of the problem through rigorous analysis and data-driven investigation.
This step is crucial, as it lays the foundation for developing effective and sustainable corrective actions.
During root cause analysis, the team employs various analytical tools and techniques, such as comparative analysis , fault tree analysis , and root cause verification experiments.
These methods help to isolate and verify the underlying causes of the problem, separating symptoms from true root causes.
Thorough documentation and verification of root causes are essential in this discipline, ensuring that the team has a solid foundation for developing effective corrective actions.
D5: Permanent Corrective Actions (PCAs)
Building upon the insights gained from root cause analysis , Discipline 5 focuses on selecting and verifying permanent corrective actions (PCAs) that address the identified root causes and mitigate the risk of future occurrences.
During this stage, the team evaluates potential corrective actions based on their effectiveness in addressing the root causes, as well as their feasibility, cost, and potential impact on other processes or systems.
Risk assessment tools, such as Failure Mode and Effects Analysis (FMEA), can aid in this evaluation process.
Once the most appropriate corrective actions have been selected, the team verifies their effectiveness through pilot testing , simulations, or other validation methods.
This step ensures that the proposed solutions will indeed resolve the problem and prevent its recurrence without introducing unintended consequences.
Detailed planning and documentation of the corrective actions, including acceptance criteria, implementation timelines, and responsibilities, are critical components of Discipline 5.
D6: Implementation and Validation
In Discipline 6, the team focuses on implementing the selected permanent corrective actions and validating their effectiveness in resolving the problem and preventing future occurrences.
This stage involves developing a comprehensive project plan that outlines the steps, timelines, and resources required for successful implementation.
Effective communication and coordination with all relevant stakeholders, including cross-functional teams and management, are essential to ensure a smooth transition and minimize disruptions.
During implementation, the team closely monitors the progress and performance of the corrective actions, gathering data and feedback to validate their effectiveness.
This validation process may involve conducting simulations, inspections, or collecting performance metrics to assess the impact of the implemented solutions.
If the validation process reveals any shortcomings or unintended consequences, the team may need to revisit the corrective actions, make adjustments, or conduct further root cause analysis to address any remaining issues.
D7: Preventive Actions
Discipline 7 of the 8D process focuses on taking preventive measures to ensure that the lessons learned and improvements made during the problem-solving journey are embedded into the organization’s processes, systems, and culture.
In this stage, the team reviews similar products, processes, or areas that could be affected by the same or similar root causes, identifying opportunities to apply preventive actions more broadly.
This proactive approach helps to mitigate the risk of future occurrences and promotes a culture of continuous improvement .
Effective implementation of preventive actions requires cross-functional collaboration, clear communication, and ongoing monitoring to ensure their sustained effectiveness.
D8: Closure and Celebration
The final discipline of the 8D process, D8, serves as a critical step in recognizing the team’s efforts, sharing lessons learned, and celebrating the successful resolution of the problem.
During this stage, the team conducts a final review of the problem-solving journey, documenting key lessons and insights that can be applied to future projects.
This documentation not only preserves institutional knowledge but also facilitates continuous improvement by enabling the organization to build upon past experiences.
Equally important is the recognition and celebration of the team’s achievements. By acknowledging the collective efforts, dedication, and collaboration of team members, organizations can foster a positive and supportive culture that values problem-solving and continuous improvement.
Formal recognition events, such as team presentations or awards ceremonies, can be organized to showcase the team’s accomplishments and highlight the impact of their work on the organization’s quality, customer satisfaction, and overall performance.
By completing the eight disciplines of the 8D process, organizations can effectively navigate complex problems, identify root causes, implement sustainable solutions, and establish a foundation for continuous improvement and organizational learning.
Integrating 8D Corrective Action with Quality Management Systems
While the 8D problem-solving methodology offers a robust framework for addressing quality issues and driving continuous improvement, its effectiveness can be further amplified by integrating it with an organization’s quality management systems .
Leveraging enterprise-level software solutions can streamline the 8D process, enhance collaboration, and foster a culture of continuous improvement.
The Role of EQMS in 8D Corrective Action
Enterprise Quality Management Software (EQMS) plays a pivotal role in supporting the successful implementation of the 8D corrective action methodology.
By utilizing an EQMS, teams can benefit from features such as:
- Standardized 8D Workflows: Pre-configured 8D workflows and templates ensure consistency and adherence to best practices, guiding teams through each discipline with clearly defined tasks, responsibilities, and timelines.
- Collaboration and Communication: EQMS platforms facilitate cross-functional collaboration by providing secure document sharing, real-time updates, and centralized communication channels, ensuring that all stakeholders remain informed and engaged throughout the 8D process.
- Data Management and Reporting: Comprehensive data management capabilities within an EQMS enable teams to easily capture, analyze, and report on quality data, facilitating data-driven decision-making and root cause analysis during the 8D process.
- Integration with Quality Systems: EQMS solutions often integrate with other quality management systems, such as corrective and preventive action (CAPA) systems, enabling seamless information sharing and ensuring that the insights gained from the 8D process are incorporated into broader quality improvement initiatives.
Automating 8D Corrective Action Workflows
One of the key advantages of leveraging an EQMS is the ability to automate 8D workflows, streamlining the process and reducing the administrative burden on teams.
Automated workflows also facilitate consistent documentation and record-keeping, which is essential for maintaining compliance with industry regulations and standards, as well as enabling knowledge sharing and organizational learning.
Data-Driven Decision-making
The 8D corrective action methodology heavily relies on data-driven decision-making, particularly during the root cause analysis and corrective action selection phases.
An EQMS provides teams with powerful data analysis and reporting capabilities, enabling them to quickly identify trends, patterns, and correlations that can inform their decision-making process.
Continuous Improvement Culture
Ultimately, the integration of the 8D methodology with an EQMS fosters a culture of continuous improvement within an organization.
The insights gained from the 8D process, coupled with the robust reporting and analytics capabilities of an EQMS, provide organizations with a wealth of data and knowledge that can be leveraged to drive ongoing process optimization and quality enhancement initiatives.
Case Studies and Examples of 8D Corrective Action
To illustrate the practical application and impact of the 8D problem-solving methodology, let us explore a few real-world case studies and examples from various industries.
These examples will showcase how organizations have successfully leveraged the 8D approach to address quality issues, resolve complex problems, and drive continuous improvement.
Manufacturing Quality Issues
In the manufacturing sector, where quality and reliability are paramount, the 8D methodology has proven invaluable in addressing a wide range of issues.
One notable example is a leading automotive parts manufacturer that faced recurring quality issues with a critical component, resulting in costly rework and customer dissatisfaction.
By implementing the 8D process, a cross-functional team was assembled to investigate the problem. Through root cause analysis , they identified a flaw in the supplier’s raw material handling processes, leading to inconsistencies in the component’s material properties.
The team implemented interim containment actions to segregate and inspect incoming materials, while also working with the supplier to implement permanent corrective actions, such as upgrading their material handling equipment and revising their quality control procedures.
Service Industry Applications of 8D Corrective Action
While the 8D corrective action approach is often associated with manufacturing, it has also proven valuable in the service industry, where quality and process excellence are equally critical.
A prominent financial institution faced challenges with excessive customer complaints related to billing errors and account discrepancies.
By implementing the 8D methodology, a cross-functional team analyzed the problem, identifying root causes such as outdated software systems, inadequate training for customer service representatives, and inefficient data entry processes.
The team implemented interim containment actions, including manual account audits and increased customer communication, while also developing permanent corrective actions, such as upgrading their billing software, revising training programs, and streamlining data entry procedures.
Healthcare and Life Sciences
In the healthcare and life sciences industries, where patient safety and regulatory compliance are paramount, the 8D methodology has proven invaluable in addressing quality issues and mitigating risks.
A prominent pharmaceutical company faced a recurring issue with contamination in one of its drug products, posing potential health risks and regulatory concerns.
By implementing the 8D corrective action process, a cross-functional team investigated the issue, identifying root causes related to inadequate environmental controls in the manufacturing facility and inconsistencies in the cleaning and sterilization procedures.
Interim containment actions included quarantining and recalling affected product batches, while permanent corrective actions focused on upgrading the facility’s HVAC systems, revising cleaning and sterilization protocols, and implementing enhanced environmental monitoring.
Automotive Industry (origin of 8D Corrective Action)
It is fitting to revisit the automotive industry, where the 8D methodology originated. In a recent case study, a major automaker faced recurring issues with engine failures in one of their popular vehicle models, leading to costly warranty claims and customer dissatisfaction.
By implementing the 8D process, a cross-functional team investigated the issue, identifying root causes related to a design flaw in the engine’s cooling system and inadequate testing procedures during the product development phase.
Interim containment actions included issuing technical service bulletins and providing temporary cooling system modifications for affected vehicles.
Permanent corrective actions focused on redesigning the engine’s cooling system, implementing more rigorous testing protocols, and enhancing communication between the engineering and manufacturing teams.
Through the 8D process and integration with their quality management practices, the automaker successfully resolved the engine failure issue, regained customer trust, and enhanced their overall product quality and reliability.
The 8D corrective action problem-solving method has proven extremely useful for handling thorny quality issues, continuously upgrading workflows, and cultivating an excellence culture in businesses.
By pairing its structured team approach with analytical tools and fact-based choices, the 8D process empowers companies to uncover root causes. It also helps implement lasting fixes and prevent repeating mistakes through establishing protective measures.
As the case studies and examples show, it’s been put to great use across many industries from manufacturing to healthcare where it originated in automotive.
Its flexibility and power have made 8D valued for boosting quality, improving customer satisfaction and staying ahead competitively no matter the market.
The Eight Disciplines methodology remains a strong tool for companies serious about excellence, innovation, and customer focus.
By wholeheartedly embracing this robust framework and blending it with modern quality practices, businesses can expertly handle complex problems. They can also unlock fresh opportunities and build the foundation for sustainable success.
In other words, don’t sleep on 8D corrective action problem-solving. Its fact-based, team-centric transformation approach strengthens any organization now and into the future.
SixSigma.us offers both Live Virtual classes as well as Online Self-Paced training. Most option includes access to the same great Master Black Belt instructors that teach our World Class in-person sessions. Sign-up today!
Virtual Classroom Training Programs Self-Paced Online Training Programs
SixSigma.us Accreditation & Affiliations
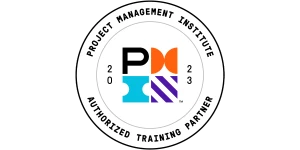
Monthly Management Tips
- Be the first one to receive the latest updates and information from 6Sigma
- Get curated resources from industry-experts
- Gain an edge with complete guides and other exclusive materials
- Become a part of one of the largest Six Sigma community
- Unlock your path to become a Six Sigma professional
" * " indicates required fields
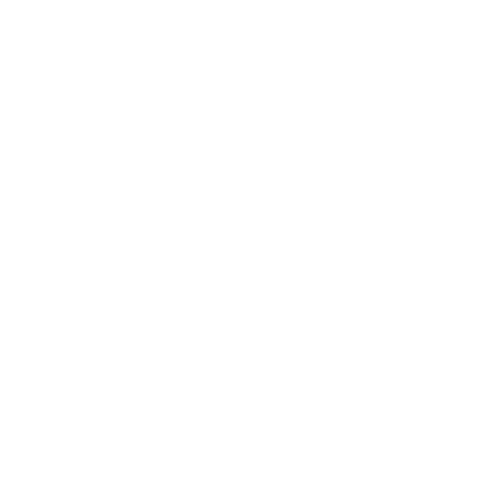
- Sign Up for Updates
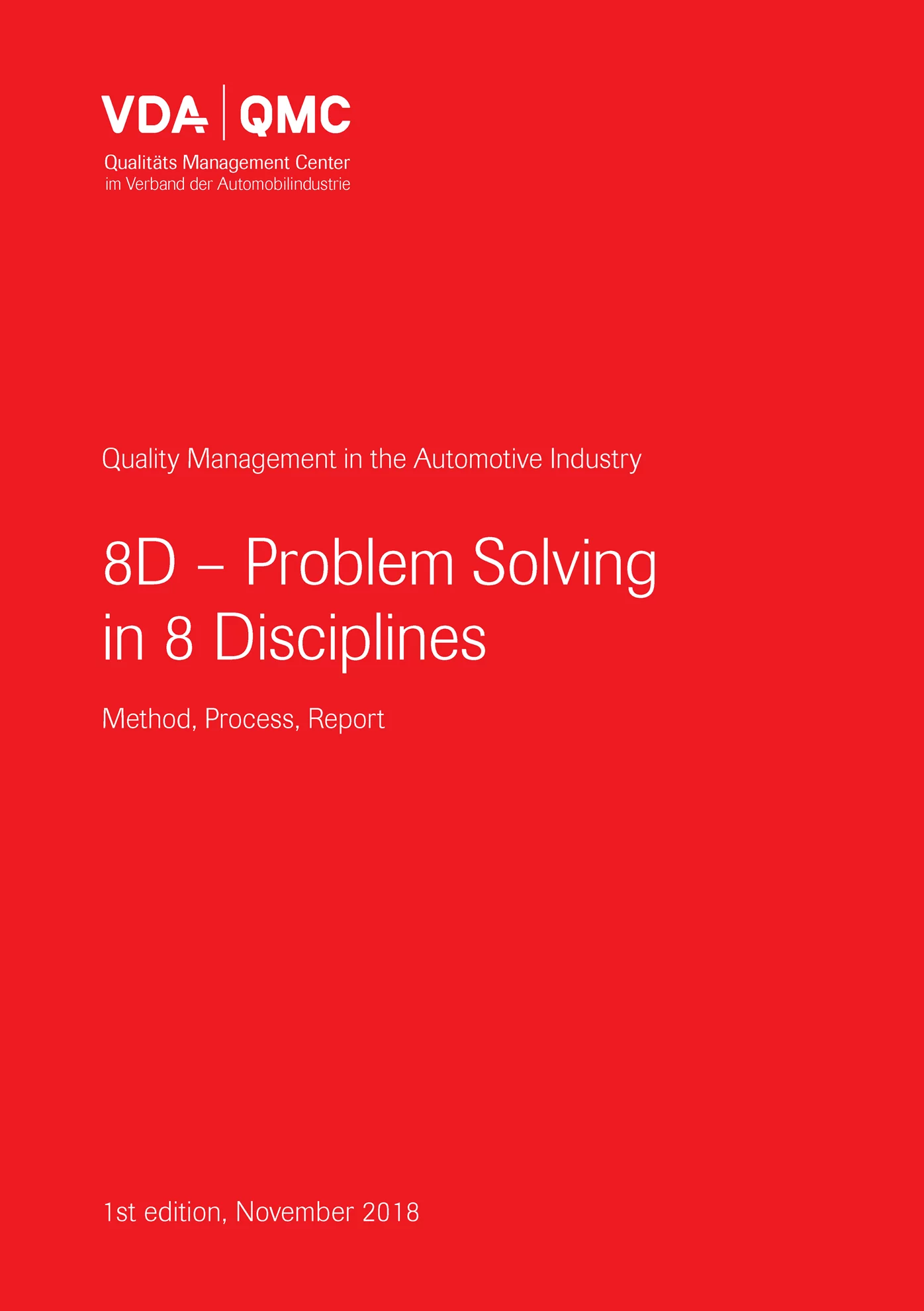
8D – Problem Solving in 8 Disciplines
£ 38.00
14 in stock (can be backordered)
Description
Additional information.

This volume describes the use of the 8D method for sustainable problem solving. It does not describe a general complaint process which contains the 8D method as a problem-solving tool.
In complaint processes, time guidelines are usually established for processing a complaint and thus indirectly also for 8D problem solving…………
…… When applying the 8D method, an appropriate sustainable solution to a problem must not conflict with timelines that are established for delivering an 8D report.
Related products
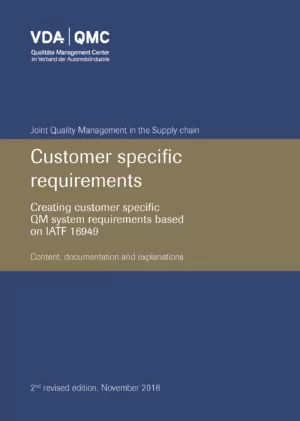
VDA – Customer specific requirement
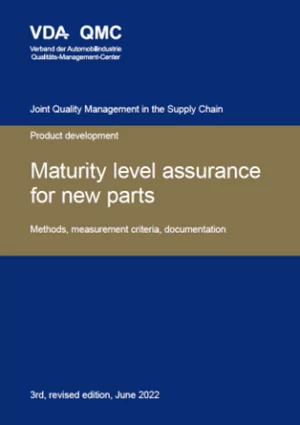
VDA – Product Development- Maturity Level Assurance for New Parts
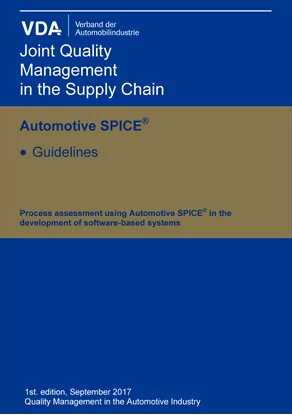
VDA – Automotive SPICE Guidelines
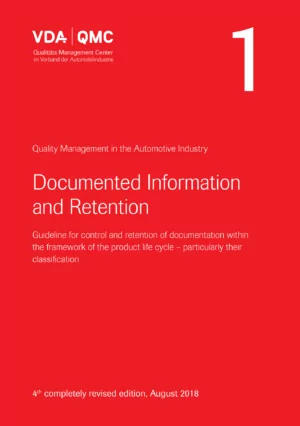
Volume 01 – Doc Info and Retention
Product categories.

Industry Forum helps major global manufacturers understand, optimise and improve both manufacturing capability and business performance. Over 250 organisations in 30 countries trust Industry Forum to deliver and maintain sustainable improvement.

Quick Links
- Consultancy
- Training Courses
- Privacy Notice
- Gender Pay Gap Statement
- Equal Opportunity Statement
- COVID-19 POLICY
SMMT Industry Forum Ltd 2680 Kings Court The Crescent Birmingham Business Park Birmingham UK B37 7YE
+44 (0)121 717 6600
[email protected]
" * " indicates required fields
For training courses, in order for us to process your enquiry as quickly as possible please fill out the following fields:
The new rules for achieving and maintaining IATF recognition - 6th edition is now available to purchase. Dismiss
Sign-up to our newsletter
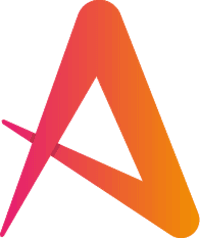
Master the 8D method of problem-solving
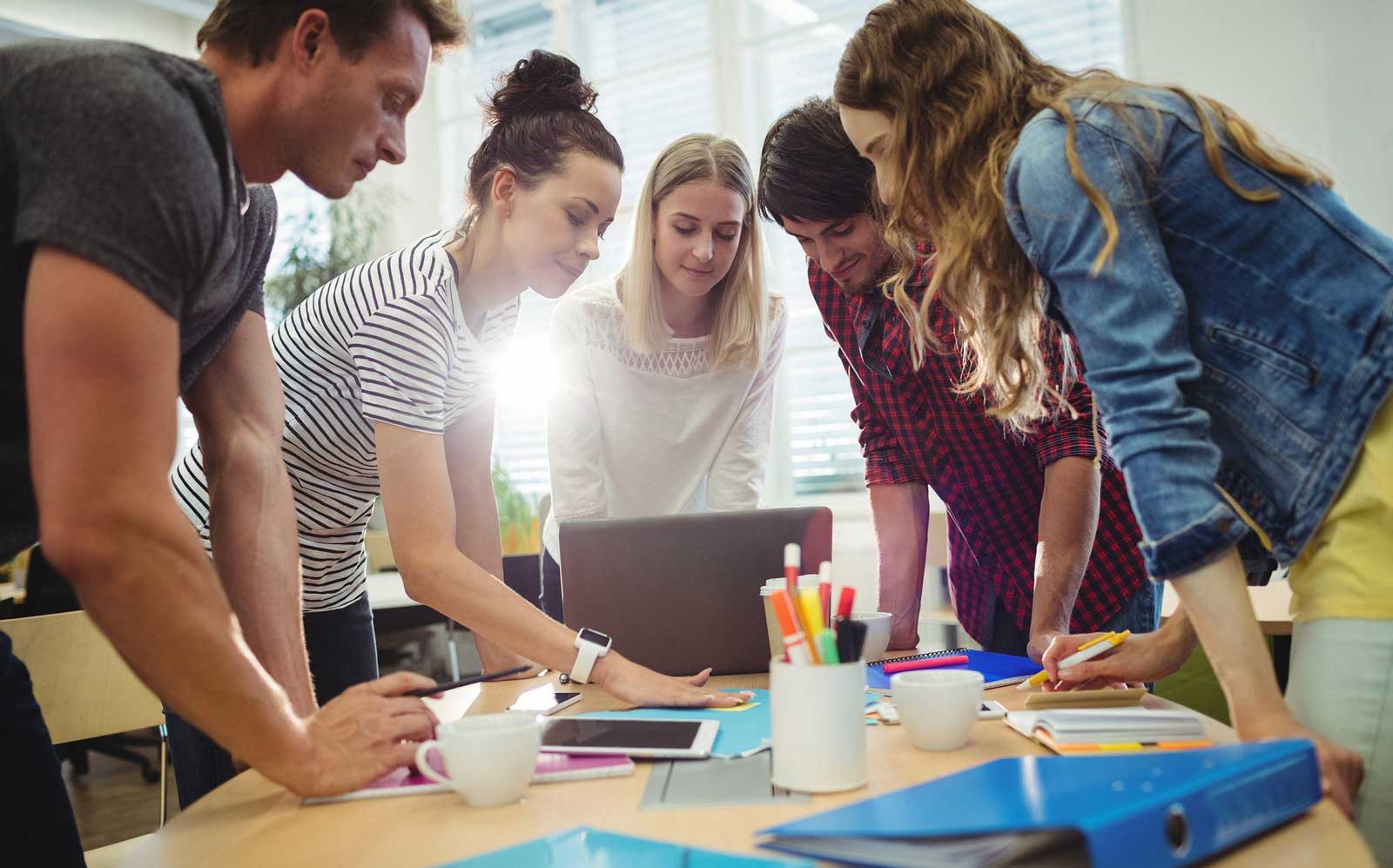
Related Articles
The 8d method was originally the brainchild of the ford motor company. the concept was developed in the 1980s and was initially given the moniker tops (team oriented problem solving) due to its emphasis on a team approach..
This approach proved to be incredibly effective, and the process has now been adopted by other companies to root out their own problems. Now known as Global 8D, the method is ideally suited to manufacturers, but it’s also been effectively used in healthcare, retail, finance and government sectors.
What is the 8D problem-solving method?
‘8D’ stands for the eight disciplines of problem-solving. Each discipline of the tool supports businesses in finding the root cause of a non-conformity and implementing a permanent solution. This detailed and disciplined approach makes it a valuable method for boosting quality and reliability within your business.
Its methodology also puts a great deal of emphasis on what is referred to as the problem-solving team. By bringing different people together, you can take advantage of their diverse experience as well as rapidly develop their individual problem-solving skills.
Other benefits include:
- Greater problem-solving efficiency
- The discovery of any necessary systemic changes
- The creation of a document trail and database outlining non-conformities and their solutions
- Better understanding of non-conformities within the business and their solutions
How do I use the 8D method?
To help you through your problem-solving journey, here is a step-by-step guide through the eight dimensions.
0D: Planning
This stage is not an official part of the eight-step process, but it remains crucial for the method to work.
Before you begin to problem-solve, you need a plan of action. Start gathering evidence on the issue, whether it is a series of customer complaints, a defective product or a process that was not carried out correctly. This will help you decide upon your team and will kick-start the investigation.
1D: Find a team
Now you have an idea of the issue, it’s time to assemble your team.
Try to choose people from different departments within the business but remember to include those who are familiar with the processes linked to the non-conformity/issue. This team can shift as your investigations continue, so be prepared to call in other expertise as you learn more about the events leading up to the issue.
To keep things moving, make sure a leader is elected. Ideally, they should be someone who is familiar with the 8D process.
2D: Problem identification
At this stage you need to set down a description of the problem. This should be fact-based and focused on information taken from business data. By doing this, you can narrow down the issue and start to rule out possible causes of the non-conformity.
To help you create an accurate description, you may like to base it on the 5W2H methodology (who, what, where, when, how and how much?).
3D: Temporary correction
Now that you have a good idea of what the problem is, you may need to put a temporary corrective action in place.
This won’t resolve the root cause of the issue, but it will help to protect your customer from receiving bad products or service from your business.
Interim measures could include stopping production or replacing defective parts, for example.
4D: Root cause analysis
We’re now getting to the business end of this process. At this stage, you can begin to identify the root causes of the non-conformity and verify them using facts gleaned from your data collection.
To help you identify the true cause of the problem, take advantage of other problem-solving techniques, such as the five whys.
The five ways is a very straightforward technique in which you ask the question ‘why’ for every answer you generate.
Here’s an example:
How to use the five whys
Problem: Water spillage in the factory.
1. First why: The water spillage occurred because the factory pipeline was leaking.
2. Second why: The factory pipeline leaked because it was damaged.
3. Third why: The factory pipeline was damaged due to poor maintenance.
4. Fourth why: The pipeline was poorly maintained because it wasn’t checked regularly.
5. Fifth why: It wasn’t checked regularly because there isn’t a maintenance schedule for the pipelines.
Root cause: A missing maintenance schedule
Other techniques include the fishbone diagram, which is illustrated below. In this example, the non-conformity was a late delivery. If using the fishbone method, you won’t necessarily fill every section – it will depend on the type and scale of problem you are investigating.
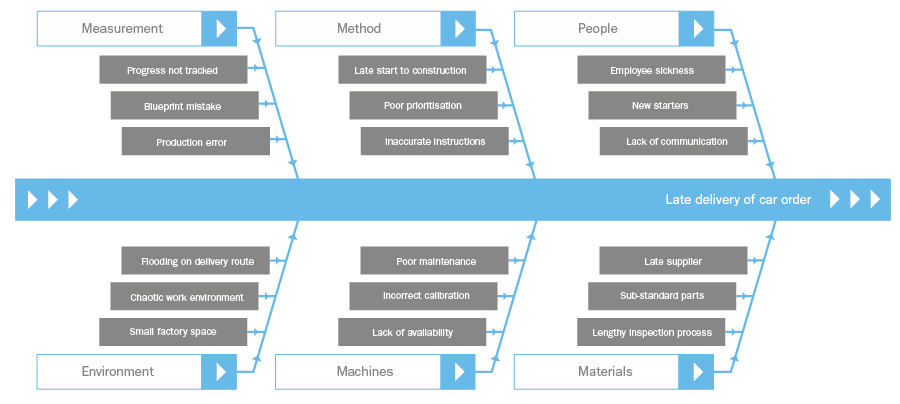
You may also like to walk through your business’ processes to discover the exact location of the root cause. In this case, a process flow diagram may be useful. This is essentially a flowchart that illustrates the relationship between major components.
5D: Permanent correction
Once you are happy that you have found the root cause of your issue, it is time to put together a permanent corrective action. This action will replace the temporary measures you put in place.
In the case of the factory water spillage, the permanent corrective action will be to create a new maintenance schedule to prevent excessive damage.
When you have a plan of what to do, you need to establish its probable effectiveness before you put it into action. Simulations or tools such as Accelerated Life Testing (ALT) can be handy for this. ALT is useful in manufacturing as it tests a product by subjecting it to extreme conditions. Once you’re satisfied that you have found the right solution, it’s time to move to the next stage.
6D: Implementation
It’s now time to implement your chosen permanent corrective action.
To implement it correctly, you need to create a project plan that covers communication to the relevant work teams and overseers as well as the steps to completion. Make sure you also decide how you will measure your success.
7D: Prevention
This stage is dedicated to making sure you prevent the non-conformity from reoccurring.
For example, in the case of the water spillage from the pipeline, the preventative action will be to communicate the new maintenance checks to the relevant team and to issue training on how to check the pipes.
Sharing your knowledge and the lessons learned during the fact-finding process is also key. Make sure the problem and its resolution are communicated to the rest of the business and update documents and your ISO processes.
You may also like to take a look at related products or procedures to see if similar problems are occurring in different parts of the business.
8D: Feedback
The last discipline is dedicated to rewarding your problem-solving team and recognising their efforts. Feed back on their performance and highlight any areas for improvement – this will help them to develop their problem-solving skills and tighten up the process during the next investigation. Once that’s done, it’s time to celebrate!
Need some extra support?
Running a management system and playing detective when it comes to non-conformities can be quite challenging when you’re juggling other business needs.
For more support or guidance, you can reach our team of experts by calling 0333 344 3646 or emailing [email protected] .
Sign up to get the latest in your inbox
- Email address
About the author
Claire Price
Content Marketing Executive
Claire worked for Citation ISO Certification between 2020 and 2022 writing creative and informative content on ISO certification and consultation to help businesses reach their potential.
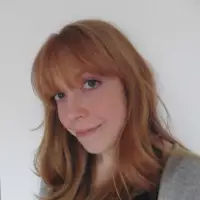
Looking for some guidance? Join us for one of our upcoming seminars!
QMS International use cookies to provide you with a better site experience, enable features and to help us understand how our website is being used.
By continuing, you consent to the use of cookies in accordance with our Cookie Policy
Allow All Cookies
Allow Strictly Necessary Cookies Only
Please Wait...

IMAGES
VIDEO
COMMENTS
The 8D problem solving process is a detailed, team oriented approach to solving critical problems in the production process. The goals of this method are to find the root cause of a problem, develop containment actions to protect customers and take corrective action to prevent similar problems in the future. The strength of the 8D process lies ...
8D is a team-based problem-solving methodology that was originally used in the automotive industry but is now used in a wide range of industry applications. It is designed to put a short-term fix in place, find the real root cause of a problem and implement a permanent long-term solution. This highly practical and interactive course focuses on ...
Practical problem solving training (8D method) Review us on. This one-day course provides a detailed understanding of a rapid, structured problem-solving process, which delivers long term solutions. Delegates will use linked tools and practical examples to become more familiar with the key stages of problem definition and solution.
The eight disciplines (8D) model is a problem solving approach typically employed by quality engineers or other professionals, and is most commonly used by the automotive industry but has also been successfully applied in healthcare, retail, finance, government, and manufacturing. The purpose of the 8D methodology is to identify, correct, and ...
8D Problem Solving Training Course Overview. 8D Problem Solving is a systematic and structured approach used to identify, analyse, and resolve complex problems within an organisation. 8D Problem-Solving methodology is crucial for organisations as it enables them to proactively address challenges, improve processes, and enhance overall ...
Eight Disciplines Methodology (8D) is a method or model developed at Ford Motor Company used to approach and to resolve problems, typically employed by quality engineers or other professionals. Focused on product and process improvement, its purpose is to identify, correct, and eliminate recurring problems. It establishes a permanent corrective action based on statistical analysis of the ...
The Ford Motor Company® developed the 8D (8 Disciplines) Problem Solving Process, and published it in their 1987 manual, "Team Oriented Problem Solving (TOPS)." In the mid-90s, Ford added an additional discipline, D0: Plan. The process is now Ford's global standard, and is called Global 8D. Ford created the 8D Process to help teams deal with ...
8D PROBLEM SOLVING. 8D is a recognised methodology for addressing concerns and opportunities for improvement. It is applicable to a broad range of problems, from those which are simple, to those which are rather more challenging. It is applicable to both manufacturing and non-manufacturing activities and is utilised by a broad range of ...
During the 8D Training participants will learn to: Describe the benefits of using the 8D model for solving problems. Identify the steps of the 8D problem solving model. Know when to apply 8D. Identify which problem solving tools are best used in each step in the 8D process. Design a Check Sheet for recording data.
Introduction to 8D Problem Solving Course Overview This problem solving training course is designed for delegates who are involved in activities and effective non conformity management for both internal and external concerns.This problem solving training course will help delegates develop relevant skills and knowledge for using problem solving tools and techniques within their organisation to ...
The eight disciplines (8D) method is a problem-solving approach that identifies, corrects, and eliminates recurring problems. By determining the root causes of a problem, managers can use this method to establish a permanent corrective action and prevent recurring issues. First introduced by Ford, the 8D method offers a consistent way of ...
A one-day course that covers the 8D problem solving techniques in context of the requirements of IATF 16949:2016. 8D problem solving is an analytical approach to investigate and identify the root cause of a concern, identify robust solutions to stop re-occurrence. Duration: 1 Day, 09:00 - 16:00.
AIE (UK) Ltd Unit 2, Ringway IndustrialEstate Eastern Avenue, Lichfield, Staffordshire,WS137SF Registered in England Number: 8058103 VAT Number: 134306837. 2 of 31 8D Scope • The 8D problem solving (Eight Disciplines) is an approach used to identify, correct and eliminate the reoccurrence of quality problems.
The Quality-One 8D problem solving training course follows the steps of 8D in a dynamic, instructor-led environment. The course describes to participants the methodologies that have proven to be best practices for effective 8D development. Each participant will be able to interact with all of the elements of the 8D process, including the use of ...
The 8D Problem Solving Format. Discipline 0: Plan. Discipline 1: Build The Team. Discipline 2: Describe The Problem. Discipline 3: Implement A Temporary Fix. Discipline 4: Identify And Eliminate The Root Cause. Discipline 5: Verify The Solution. Discipline 6: Implement A Permanent Fix. Discipline 7: Prevent The Problem From Recurring.
Global 8D Training. Global 8D (G8D) problem solving training and consultancy uses 'Root Cause Analysis (RCA)' in developing permanent corrective actions for problems. Our course has assisted clients in meeting the NADCAP 'Root Cause Corrective Action (RCCA)' training requirements.. The course takes a tutor led learning-though-doing workshop approach and can be delivered over 1 or 2 ...
8D problem solving is an 8 step process for to investigate and identify the root cause of a concern, identify robust solutions to stop re-occurrence. Whilst this problem solving methodology has been developed by the automotive sector it is also widely used outside of the automotive sector too. The course utilises case studies so that delegates ...
The 8D approach is a problem-solving methodology that follows eight disciplines to help teams identify, correct and eliminate recurring issues in manufacturing. Sam Bowen uses 8D to solve a variety of manufacturing challenges. It looks intuitive at first glance: you plan your approach, describe and contain the problem, verify the root cause ...
Root Cause Corrective Action Using the 8D Process Eight Disciplines (8D) Problem Solving is a method developed at Ford Motor Company used to approach and to resolve problems, typically . employed by engineers and quality professionals. Focused on product and process improvement, its purpose is to identify, correct, and
This is where the 8D corrective action problem-solving method earns its stripes. It was developed by Ford in the 80s and has since spread widely across manufacturing, healthcare, aerospace, and more. The 8D approach is a methodical process combining pros from different parts of the company, analytical tools, and fact-based decision-making.
8D - Problem Solving in 8 Disciplines. £ 38.00. 14 in stock (can be backordered) Add to basket. ISBN: N/A SKU: 110186 Category: VDA Books, Standards and Publications. Description.
The 8D method was originally the brainchild of the Ford Motor Company. The concept was developed in the 1980s and was initially given the moniker TOPS (Team Oriented Problem Solving) due to its emphasis on a team approach. This approach proved to be incredibly effective, and the process has now been adopted by other companies to root out their ...
PMI2014. The team should be cross functional and include members from all affected parties. D 4 Root Cause analysis. Conduct an analysis of the root causes of the problem. Do the corrective actions work? D 4 Root Cause analysis. Conduct an analysis of the root causes of the problem.